锻造是一种生产技术,可为汽车应用的动力总成、底盘以及越来越多的乘用车车身提供强度优异的部件。通常在压应力作用下多次变形的材料是细晶粒的,其中的夹杂物要么破碎,要么沿着载荷的方向移动。这会产生高强度、同时具有高韧性和延展性的部件。汽车行业当前和未来的一系列零件(带花键或齿轮的转子轴、传动零件、耐磨轴承部件、安全相关底盘部件)只能通过锻造来实现。
由于乘用车中的原材料(主要是钢和铝)是由矿石或废料生产的,并且根据锻造、材料和热处理技术,它需要经历一个或多个加热过程,因此这些零件是能源密集型的,并且,根据目前的技术水平,具有更高的CO2排放量。然而,德国锻造行业正在承担自己的责任,积极减少CO2的排放。
1.初始情况和解决方法
德国锻造行业是一个能源密集型行业,预计能源需求为3 TWh(天然气和电力),不考虑所使用的原材料[1]。根据锻造方法,典型的工艺顺序可能由以下步骤组成,每个步骤都可以执行多次:输入材料(钢、铝、钛、镁、黄铜)的生产和供应、切割、预涂、加热、多级单步或渐进锻造、热处理和机械加工。
如今,能源供应总是与CO2排放相关。《欧洲绿色协议》的“气候”措施规定,到2030年,温室气体净排放量比1990年的水平至少减少55%,并呼吁到2050年实现气候中和[2]。汽车行业,目前已经在推动供应链解决生产中二氧化碳排放的问题。一方面,要求包括量化供应部件的产品碳足迹(PCF);另一方面,呼吁采取持续措施减少PCF。
德国锻造行业正在与其合作伙伴行业一起积极应对这些挑战。于是,2020年12月,德国锻造协会启动了Nocarbforging 2050项目。在初始阶段,工程服务提供商promalys与合作伙伴GreenData和Herlanco一起创建并进一步开发了基于网络的软件计算工具。
2.生态足迹计算工具
在Nocarbforging 2050项目的第一阶段,正在开发“Fred”软件工具。这代表锻造足迹减少工具,用于计算锻造零件的PCF。来自锻造行业以及合作行业的50家公司参与其中。该软件工具被设计为网络应用程序。要计算PCF,需要一些基本数据:组件质量、使用的功率组合、起始材料的PCF以及一些其他信息。此外,输入产品的单独处理顺序。对于这些过程,电能、气体和其他材料的具体消耗量来自数据库。此外,还针对各个流程指定了不可避免的材料损失。为最终产品排放。
在第一阶段,从众多参与公司获得了有关电力和天然气消耗以及典型材料损失的数据,并将其存储在软件工具中。虽然肯定总是有改进数据的潜力,但“Fred”目前已经为金属加工工艺提供了比用于PCF计算的其他数据库更准确、更详细的分析。图2显示了登录网页、基本数据和处理顺序的输入以及淬火和回火万向节的PCF计算结果示例。这种典型闭式模锻零件的结果反映了许多锻造零件的基本特征。所使用的起始材料占PCF的最大比例。其次是热处理(例如淬火和回火),然后加热到锻造温度。
影响比例的一个因素是钢材是否来自粗钢( crude)或电炉钢(electric steel route),或者是否使用铝等。其他影响变量包括锻造温度以及锻造后是否进行任何热处理。
3.制定减少CO2排放的想法
减少甚至避免CO2排放的途径涉及绿色电力,即可持续发电。这使得通过使用绿色氢的直接还原路线、通过废电路线或采用全新方法来生产不排放CO2的钢铁成为可能[3]。还可以想到电(再)加热工艺,例如用于自由锻造和轧制,或者用于锻造厂或钢厂中的热处理。或者,可以使用氢气[4],或者由电力合成产生的甲烷。同样,闭式锻造中的加热过程现在大多是感应式的,因此绿色电力可以避免CO2这里的排放也一样。然而,同样明显的是,完全放弃化石能源进行材料生产将需要大量投资和运营成本。同样,将当今的基于气体的加热或热处理工艺转换为氢气或电力也将产生高昂的成本。因此,开发额外的路径来提高材料和能源效率非常有意义。这将至少可以部分抵消未来更高的能源成本,从而使向无CO2制造的过渡更加经济。
通过计算各种锻造工艺链的CO2排放量,为评估如何减少排放的想法奠定了基础。因此,“Emma - 锻件的零排放制造”研讨会期间,产生了51项减少锻造过程中CO2排放的初步想法。这些想法根据以下标准进行分类:CO2的百分比节省潜力、成熟期(可以直接实施,可以在ZIM(中小企业中央创新计划)项目中开发,可以在BMBF(德国联邦教育和研究部)项目中开发,或者在BMWi(德国联邦经济事务和气候行动部)项目)、实现时间表和实施成本。此外,这些想法还根据主题领域进行分类:材料生产、材料特性、热处理、锻造工艺、基础设施优化和其他工艺。
这些想法表明CO2减排潜力在3%到50%之间。在某些情况下,可以同时将多种想法应用于一个组件,从而增加节省潜力。与想法成熟度相关的时间范围从立即可行到六年以上的开发期。然而,这个想法要想完全运用到实践中,肯定还需要几年的实施时间。所产生的想法的实施成本同样差异很大。从减少CO2排放的潜在解决方案的初步快照来看,很明显,对CO2的合理评估节省开支(例如使用“Fred”)对于优先考虑最有效的想法是必要的。
4.优先考虑最有效的想法-从材料生产到基础设施
该材料对锻造产品的碳足迹贡献最大。因此,努力使用具有较低PCF的材料是减少锻造部件的CO2排放的非常有效的措施。在这里,市场上已经有一些可以利用的解决方案。例如,一家瑞典钢铁制造商从2022年初开始提供无CO2长钢的选择。无CO2指范围1和2(图2),其中部分减排是通过碳补偿实现的。然而,通过适当的基础设施措施,预计未来几年此类抵消的使用将大幅减少[5]。
一家德国钢铁制造商提供一种绿色钢材,这种钢材在电弧炉中使用可再生能源的电力熔化。因此,非合金工程钢和高合金钢的PCF(范围1和2,图2)降至约50%[6,7]。其他钢生产商也在积极降低其产品的碳足迹[8]。
从图2饼图的“淬火和回火”部分可以看出,部件的热处理是CO2排放的第二大驱动因素。在锻造材料方面,过去20年取得了许多进展,旨在用锻造热冷却代替淬火和回火工艺。改进的弥散硬化钢、贝氏体钢[9]甚至空气硬化马氏体[10]均可用于此目的。利用这些新的锻造材料,可以降低生产中的CO2排放量,并且在大多数情况下还可以降低成本。
此外,如果锻造公司也使用效率更高的再生电能[11],或者通过预成型操作或更精细调整的锻造工艺来节省输入材料,则可以优化PCF。
图4显示了前面提到的和已经可用的输入变量或技术可能性如何导致CO2足迹的显着减少。使用万向节组件作为示例再次演示这一点。减少至27%成为可能。在这种行业竞争前合作的背景下,显然不能讨论任何成本问题。主要是CO2减排取决于气候中性电能和充足废钢或直接还原铁的供应。类似的关系对于铝来说也是有效的——尽管彼此之间的比例不同。然而,对于实施这些想法也至关重要的是,在产品开发过程中整个供应链中涉及的所有各方之间保持一致的技术合作。
5.总结与展望
如今,利用市场上提供的选项和技术可能性,已经可以显着减少锻造部件的产品碳足迹。这主要可以通过无CO2电能来实现,尽管目前还没有达到实现材料和锻造行业完全转变所需的数量。需要对发电和其他基础设施(特别是原材料行业)进行大量投资,以显着减少CO2排放。从当前的角度来看,不可能为此指定确切的时间表。因此,提高材料和能源效率的进一步想法是必要的,并且目前可用于实现CO2的大幅减少尽快并以经济可行的方式排放。锻造行业正在积极满足这些要求。毕竟,通过这样做,他们希望并且能够确保材料生产和加工的价值创造将在未来继续在德国和欧洲发生。
来源:汽车材料网翻译整理
注:本文版权归原作者所有,文中观点仅供分享交流,不代表本公众号观点和立场。如涉及版权等问题,请您告知,我们将及时处理。
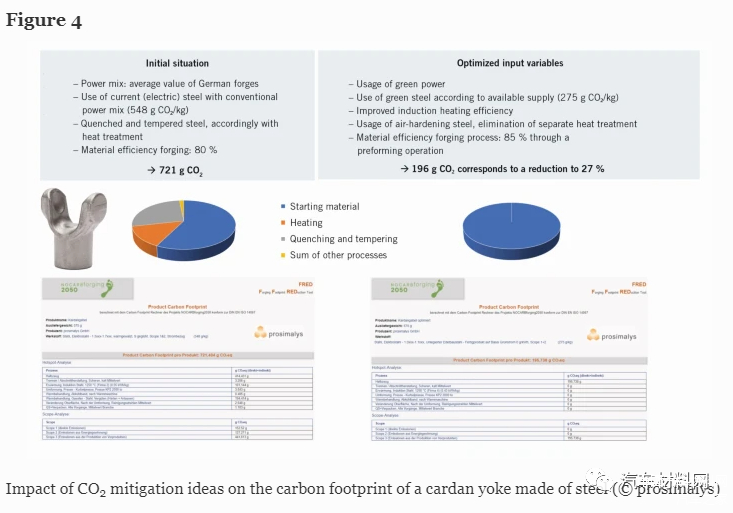