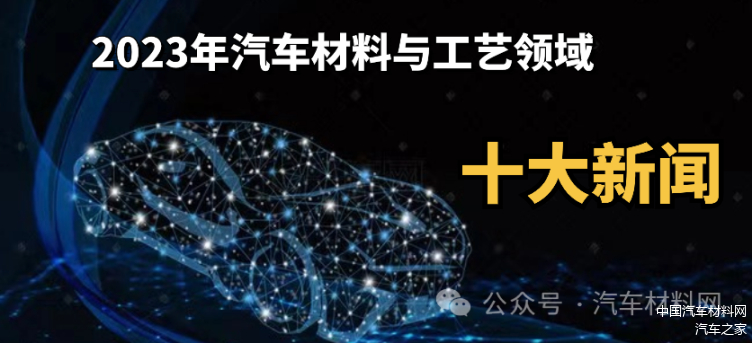
材料与工艺技术是实现汽车高品质发展的基石,无论是电动化还是智能化,都离不开材料与制造工艺技术的支撑。当前,国内外汽车材料及制造工艺技术的开发与应用得到了快速的发展,汽车创新材料及先进制造工艺技术的应用对于改善汽车产品的性能,提高汽车产品的市场竞争力具有重要的作用。为了更好地满足汽车行业的对材料和工艺技术的需求,尤其是新能源汽车快速发展催生的新需求,中国汽车材料网自2017年起开始出版《汽车材料与制造工艺年鉴》,多年来受到行业的普遍欢迎和广泛的好评。
年鉴将及时跟踪上一年度中国汽车材料与制造工艺等方面发展情况,全面记述汽车材料与制造工艺的技术发展、企业动态,以及相关的产业统计数据,成为了中国汽车材料与制造工艺界的史实性、连续性、综合性的工具书,为全国汽车产业上下游的规划、科研、生产、销售及新产品开发等提供较好的指导与服务。
时间飞逝,转眼间2023年已成为过往。2024版《汽车材料与制造工艺年鉴》编制工作接近尾声,即将在3月初面向全行业出版发行。
回顾2023年度汽车行业发展,中国汽车材料网在网站和微信平台点击量较大的国内外热点新闻基础上,选出过去一年汽车材料与工艺领域的热点新闻与重点技术进展,结合行业专家的意见,评选出过去一年的十大新闻,评选结果如下:
01东北大学Science发文!揭示2GPa汽车超高强钢增韧机理
据东北大学消息,2023年1月13日,东北大学轧制技术及连轧自动化国家重点实验室王国栋院士/袁国教授研究团队在国际顶级期刊Science上以“Ductile 2-GPa steels with hierarchical substructure”为题,发表了在超高强钢铁材料增塑机制及组织创新设计方面的最新研究成果。
研究团队创新提出“马氏体拓扑学结构设计+亚稳相调控”协同增塑新机制,成功制备出系列低成本C-Mn系新型超高强钢,打破了超高强钢对复杂制备工艺和昂贵合金成分的依赖,也突破了现有2000 MPa级马氏体高强钢抗拉强度—均匀延伸率的性能边界。同时,提出简单高效的制备工艺路线,构筑出一种全新的拓扑学双重有序排列的马氏体和多尺度亚稳奥氏体的纳米级多层次组织结构。该组织结构通过在变形过程中诱发板条界面(in-lath-plane slip)位错滑移、界面塑性和相变诱发塑性(TRIP)等多种增强增塑机制,促使材料具有持续较高的加工硬化能力,大幅度提升其强度和塑性,实现了1600~1900 MPa屈服强度,2000~2400 MPa抗拉强度和18%~25%均匀延伸率的极致性能。该研究不仅对于钢铁材料,也为其他超高强塑性金属材料的开发制备提供了新的研究思路。
02鞍钢低密度钢产品全球首发 技术成果达到国际先进水平
据中国金属学会及汽车材料网消息,经行业专家组成的评委会评审,鞍钢股份、燕山大学、太原理工大学共同研究开发的“先进高强汽车用钢全流程制造工艺与质量综合控制技术”项目被认定为整体达到国际先进水平。其中,低密度钢系列产品实现全球首发,先进高强汽车用钢轧制全流程板形高精度稳定控制技术达到国际领先水平。
鞍钢与客户通过冲压模拟和零部件实际冲压实验,开展了低密度高成型性冷轧高强汽车钢在白车身、电池包、座椅等汽车部件上的优化设计和成型模拟研究。他们发现通过优化结构设计和低密度高强汽车钢的使用,能够实现汽车零部件减重5%至10%,吸引了国内外众多汽车厂家的关注和兴趣。未来,鞍钢将开展冷轧、热镀锌、热轧酸洗等低密度高强汽车钢系列产品开发和轻量化应用技术研究,为汽车轻量化提供更加创新的解决方案。
03宝钢低碳钢(BeyondECO®-30%)量产供货第一卷正式下线
据宝钢消息,2023年3月27日,国内首个量产供货的低碳排放汽车板产品、宝钢量产供货的第一卷低碳钢(BeyondECO®-30%)在宝山基地1550电镀锌机组正式下线!宝钢量产供货第一卷电镀锌低碳钢(BeyondECO®-30)严格遵守相关减碳、降碳措施和生产工艺路径,经宝钢产品碳管理专业团队初步核算该卷电镀锌低碳钢的减碳强度与原零件非减碳路径生产的钢卷减少超过30%,并且经宝钢内部评估钢卷质量等关键指标全部满足目标零件的要求。
本次量产供货第一卷宝钢低碳钢产品成功下线,是宝钢打造新能源车整体解决方案品牌SMARTeX,以宝钢汽车板QCDDS为品牌基因,赋能汽车用户,与北京奔驰探索生产制造低碳绿色钢及产品取得的重大突破。
04宝钢1.5GPa级别冷冲压吉帕钢量产零件中国首发成功
据宝钢消息,2023年11月9日,国内首个面向量产采用1.5GPa吉帕钢®冷冲压零件成功试冲,吉帕钢®HC1000/1470DP是宝钢股份的全球首发产品之一,是双相钢系列目前最高强度,与1180DP、1310DP等超高强度双相钢相比,强度等级提升了10%~30%。该产品填补了国内在该强度级别品种冷成形汽车板的产品空白,并兼具以下优秀综合特性:超高强度、较高延伸率、良好弯曲性能、优良焊接性能、低延迟开裂风险。
宝钢汽车板产销研团队从一贯制上实现了该高性能材料的稳定化制造,使之在抗拉强度达到1500MPa的同时,仍具有优秀的延伸率表现,尤其适合有强度要求、且有局部特征的梁类零件,为保险杠、防撞梁、座椅横梁、顶盖横梁等对焊接性和安全性要求较高的关键零件提供了新的材料和解决方案;同时也为车身安全件进一步减重提供空间,满足汽车行业轻量化和低碳化对新材料的需求。
05埃安“钢铝混合车身”技术 荣获中国科技界汽车“奥斯卡”奖
据AI汽车网消息,5月16日,中国汽车行业内最高级别的科学技术奖、被誉为中国科技界汽车“奥斯卡”的中国汽车工程学会科学技术奖颁奖典礼在北京举行。由广汽集团牵头,联合广汽埃安与大连理工大学共同完成的“电动汽车轻量化钢铝混合车身研发与制造关键技术”项目荣获科技进步奖二等奖。
项目运用新材料和新工艺,将轻量化做到极致,同时大大提升了电动汽车的节能表现,对行业升级和社会绿色发展意义深远。该项目的成功不仅在于科学技术的进步,还在于它改变了人们的生活,让人人都能体验到豪车般的享受。项目成果率先应用在AION LX、AION V车型,并推广到广汽三菱及合创等合资车型,市场反响热烈。
06现代汽车发布全新车漆低温固化涂装技术,助力减少碳排放
据现代汽车消息,现代汽车公司发布了一项新的涂装技术,该技术可大幅降低汽车涂装过程中的能耗,并最大限度地减少碳排放。
汽车涂装过程主要通过四个步骤完成:前处理、底涂、中涂和面涂。在这个过程中,通过高温处理使涂层硬化的过程被称为“固化过程”。该涂装技术,在保持原有的涂装质量的前提下,在90℃的温度下用20分钟进行面漆固化工序,而之前的固化工序是在140℃温度下固化20分钟。现有的油漆含有三聚氰胺,只能在约140℃或更高温度下固化,但现代汽车公司新开发的油漆使用了异氰酸酯代替三聚氰胺,后者在90℃或更高温度下就可以固化。在汽车生产过程中,喷漆工序消耗的能源最多(约占43%),也被认为是碳排放量最大的工序。如果这项喷漆技术实现商业化,公司预计该行业的碳排放量和燃气消耗量将各减少40%。
07国内首创!红旗将玄武岩纤维首次引入汽车内饰产品
据红旗汽车消息,红旗汽车牵头开展汽车用环保型玄武岩纤维复合材料开发及产业化研究,打造原创产业共性技术,首次将玄武岩纤维引入汽车内饰产品,践行绿色低碳理念,发挥健康、轻量化优势。
玄武岩纤维源于天然岩石,直接熔融拉丝而成,是一种新型绿色高性能无机材料。面向汽车用材趋势,挖掘高价值应用场景,聚焦内饰产品关键性能需求,首创开发环保型玄武岩纤维复合材料。以材料-结构-工艺一体化开发为手段,加速实现其在行李箱盖护面、侧护面、包裹架护板等部件的首批应用;下一阶段可在门内板、座椅背板等内饰部件深度开发;通过优化材料及工艺,未来可拓展至车身底护板等外饰部件,应用前景广阔,预估可达百亿级产业规模。
玄武岩纤维复合材料开发为国内首创技术,通过突破低气味玄武岩纤维浸润改性技术、玄武岩纤维复合材料配方和工艺优化技术,已实现中试材料开发,并基于中试材料完成了行李箱盖护面等样件的试制,实现零件降重20%以上,原生气味≤3.0分。下一步将开展整车性能验证,并同步完成正式系列化材料开发,结合过程研究数据,形成标准和规范,支撑高品质应用,助推产业化落地。
08麦格纳推出业界首创、100%熔融可回收泡沫和装饰座椅解决方案
据盖世汽车消息,2023年10月11日,麦格纳(Magna)宣布推出业界首创EcoSphere™产品系列,利用单一材料聚对苯二甲酸乙二醇酯(PET)以及该公司创新的100%熔融可回收泡沫(Melt Recyclable Foam)和装饰(Trim)系统,避免在垃圾填埋场处置座椅泡沫垫和装饰套。麦格纳新EcoSphere产品系列由可持续装饰材料、装饰垫、结构和泡沫组成。
利用麦格纳在泡沫化学、装饰制造、工艺和工具集成方面的专业知识,该产品系列是一种无缝且经济的解决方案。此外,100%熔融可回收泡沫和装饰技术可确保座椅材料的外观和触感保持符合行业标准,同时显著减少对环境的影响。
麦格纳EcoSphere Trim Foundation是100%熔融可回收泡沫和装饰技术的重要组成部分。每款座椅都会采用装饰基础。EcoSphere Trim Foundation会被层压到装饰材料的背面,以提供支撑和清爽的外观。通过利用回收材料和生物基材料、实施节能制造工艺并考虑报废管理,麦格纳的可持续座椅方法为其净零目标做出了贡献,不仅减少了温室气体排放,还降低了麦格纳产品的碳足迹。
09 2万吨!哪吒汽车开研全球最大的汽车压铸设备
据搜狐新闻消息,12月18日,哪吒汽车与力劲集团签署战略合作协议。根据协议,双方将共同研发全球最大的20000+吨压铸设备,这一合作将刷新汽车行业和压铸设备行业的纪录。
一体化压铸已成为新能源汽车制造商争夺的焦点,并且是滑板底盘生产所需的一项革命性制造技术。与传统制造方式相比,一体化压铸通过特大吨位的压铸设备将原本分散的零部件集成在一起。它可以显著减少汽车的部件数量,降低制造成本,并将汽车底盘的制造时间从1-2小时缩短至1-2分钟。此外,它还可以减轻车辆重量、提高车辆舒适性等。
哪吒汽车率先抢占20000+吨级压铸技术的突破性优势,对汽车制造业缩减成本具有重要意义,并带来产品研发层面的竞争升级。此次合作标志着力劲集团在汽车制造业中占据重要地位,同时也为哪吒汽车带来了更多机会和挑战。
10采埃孚开发无磁免稀土高效电机
据环京津新闻网报道,全球性技术公司采埃孚集团宣布开发出一款无需磁性材料的驱动电机。与当今单独励磁同步电机的无磁概念不同,采埃孚内转子式感应励磁同步电机(I2SM)可通过转子轴内感应励磁机传递磁场能量,在确保电机独具紧凑性的同时实现最大功率和扭矩密度。这种先进的励磁同步电机迭代款是永磁同步电机的优化方案。目前,后者在电动车中的使用最广泛,但均需稀土材料才能生产。根据内转子式感应励磁同步电机的特性,采埃孚正在制定新标准,以实现电机的极高生产可持续性,及强大的功率输出和电机效率。
了解更多汽车材料与制造工艺发展状况,敬请关注2024版《汽车材料与制造工艺年鉴》!
来源:汽车材料网