比亚迪历时5年,耗资百亿推出了纯电整车架构平台化的全新e平台3.0。从底盘层、高压层、低压层、车身层,全面整车架构开发,突破了电动车的性能短板,赋予电动车高级别的智能进化能力,彻底释放智能、电动化潜力。为智能电动汽车的蓬勃发展,提供了绝佳的基础平台。
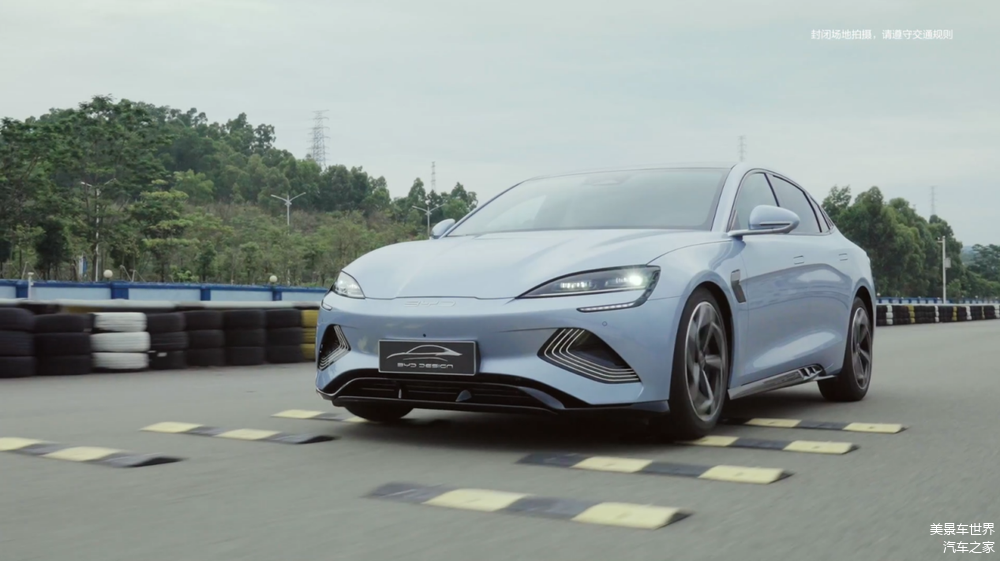
e平台3.0不仅能打造一款有极致体验的车型,也能孵化各种尺寸的智能电动汽车,从A级车到D级车,全面覆盖。目前,基于e平台3.0已有三款产品上市,未来还将在多个品牌陆续推出新车型,以满足更多用户需求。
人车融合 极“智”体验
智能驾驶的终极形态,是解放驾驶者双手,辅助驾驶者与乘员,规避潜在道路或行驶风险,实现“无死角”的安全自动驾驶。比亚迪始终以“安全无死角”为标准进行车型产品开发,从软硬件综合且深度融合、持续迭代安全驾驶与智能驾驶,始终保持在行业领先水平,并不断迭代。e平台3.0是比亚迪对智能安全驾驶能力的再一次赋能。通过充分发挥车辆本身极佳的控制能力,e平台3.0能够轻松将路面感知能力和视觉感知能力有机融合,打破过往的算法局限。
在安全的前提下,从域控制电子电气架构、车控操作系统BYD OS以及积累的闭环生态能力输出稳定可靠的底层能力,提升智能驾驶体验。与此同时,e平台3.0预留了各类自动驾驶的硬件接口,可灵活配置全球最顶尖的自动驾驶方案,定制个性化出行体验。
自主研发的车用操作系统BYD OS
车控操作系统OS (Operating System),采用面向服务的软件架构(SOA),体现了高内聚、低耦合、高可靠、低延时等技术特点,并对车路云网一体化的未来应用提供了方案和接口,实现了多项整车功能安全技术,可以充分满足车身电子、底盘控制、动力系统、智能驾驶等多领域的应用。车控操作系统OS是底层硬件与用户沟通的桥梁,需要整合各类型软件应用以及适应中央集中式电子电气架构的必要基础,是汽车数字化转型的关键。
比亚迪自主研发的基于车用场景的操作系统BYD OS,使用确定时延引擎和高性能IPC两大技术解决现有系统性能不足的问题。确定时延引擎可在任务执行前分配系统中任务执行优先级及时限进行调度处理,优先级高的任务资源将优先保障调度,应用响应时延降低25.7%。搭配全新的域控制电子电气架构,实现软件与硬件的完全解耦、支持高级别驾驶开发的核心能力,功能迭代周期缩短70%;可实现应用程序的跨硬件的即插即用,软件跨平台通用,高效OTA使智能电动汽车持续进化,常用常新。
iTAC智能扭矩控制系统
iTAC是针对电动车特性打造的车辆扭矩控制系统,电动车上所采用的电机则可以更快采集轮端信息,通过电机旋变传感器,轮端每一圈可分成4096个采集位,信息采集速度和精度大大提升。iTAC较以往提前50ms以上预测到车轮轮速的变化趋势,相比于传统控制策略,识别精度提升了300多倍,汽车动力的控制精度与速度得以大幅提升。
iTAC在提前预判的基础上针对电机响应速度快、转速调整更精确的特点,提供了转移扭矩、适当降低扭矩和输出负扭矩等多种方式。在车辆即将发生打滑时,iTAC可以将低附着车轮扭矩全部或部分转移到有抓地力的车轮上,使车辆恢复稳定,从而不触发或者减少触发ESP功能,提升驾驶稳定性,做到车辆安全性能提升的同时,同时提升驾乘更舒适和驾驶极限。
自主研发高性能SiC电控
功率半导体作为电力系统的重要组成部分,是提升能源效率的关键因素。高电流密度、高效率的SiC是公认优良的新一代电控功率芯片。e平台3.0攻克了高功率密度SiC芯片可靠封装的难题,并成功开发出全球首款量产的SiC功率模块控制器,实现SiC功率模块完全自主设计、封装和制造,具备完全自主的知识产权。
e平台3.0电驱动系统搭载的高性能SiC电机控制器,其SiC功率模块的规格是1200V-840A,具有高效率、高耐压与强过流能力。与传统IGBT控制器相比,SiC电控开关损耗降低70%以上,最高效率达99.7%;SiC电控的峰值功率可达230kW以上,功率密度提升近3倍。同时,SiC使用了高性能氮化硅AMB板和全新的银膏烧结工艺,并集成了高灵敏NTC传感器,使得e平台3.0的SiC功率模块和控制器水平在世界遥遥领先。
宽温域高效热泵系统
电动车低温续航里程衰减的原因,除了电池本身活性降低后能量下降外,另一个主要原因是能耗增加。与燃油车相比,纯电动车由于没有发动机本身冷却系携带的大量热量,所以需要消耗大量电池能量来维持乘员舱采暖及电池温度,导致冬季续航里程衰减。
为了更高效的利用能量,行业尝试利用热泵来吸收空气的热量以降低能耗,因为热泵是一种可以将低位热源的热能强制转移到高位热源的装置。但受限于134a冷媒的搬运能力,在零下10℃,热泵的制热效率会大幅降低,甚至无法有效工作。
通过热泵将乘员舱、动力电池、驱动总成的深度集成的热泵系统架构,驱动总成的余热回收后为热泵提供高品位辅助热源,使得热泵在零下25℃也能够完全满足乘员舱采暖需求。首创冷媒直接冷却加热式的电池热管理,减少能量传递环节,进一步提升能量利用效率。为解决热泵低温下性能差的痛点,全新e平台3.0,首创驱动总成充电和驱动工况主动产热的黑科技。即使在零下40℃的极端天气,热泵仍然能够正常工作,降低采暖能耗损失。同时有效提高电能到热能的转换率,低温续航里程提升超20%。全面提升续航性能,缓解低温续航衰减的焦虑,是让用户可以随时随地放心开出门的电动车。
e平台3.0热泵系统具有11种工作模式,包括单电池加热模式、单乘员舱采暖模式、乘员舱采暖+电池加热模式、单电池冷却模式、单乘员舱制冷模式、乘员舱制冷+电池冷却模式、乘员舱采暖除湿、乘员舱采暖除湿+电池加热、乘员舱采暖除湿+电池冷却、乘员舱制冷+电池加热模式、乘员舱加热+电池冷却模式,覆盖用户所有采暖制冷使用场景,在冬季制热工况下能效比(COP)可达2~4,能效多倍于市面上普遍使用的PTC加热方式,具备-30~60℃的宽温域工作的能力。
CTB电池车身一体化技术
CTB技术以“电池车身一体化”为核心设计理念,实现了40000+N·m/°的高扭转刚度,大幅提升整车动态响应,赋能操控性能;同时作为车身的一部分参与传力和吸能,实现整车安全性能的大幅提升,让e平台3.0具备全球超五星安全的能力。e平台3.0作为下一代纯电平台的技术标杆,着重聚焦车身安全性从底层优化,开创性提出CTB(Cell to Body)电池车身一体化技术。
1)刀片电池,CTB技术最佳搭档:
CTB技术在“蜂窝“中找到灵感,结合刀片电池独有的长方体结构和超级强度,衍生出“类蜂窝铝”结构,带来电池成组技术里程碑式的革新,通过将刀片电池包与车身刚性连接,二为一形成完整体,并取消传统的车身地板设计,将地板(电芯上盖)-电芯-托盘三者与车身集成,形成高强度的“整车三明治”结构。刀片电池既是能量体,也是结构件,成为车身传力和吸能结构的一部分,在碰撞工况下,车身具备充足的吸能空间及更顺畅的能量传递路径,乘员舱形变大幅减小,给乘客创造了坚固安全的环境,逐步实现事故“零”伤亡。
2)一体设计优化传力路径,碰撞保护硬实力:
CTB技术采用车身地板纯平设计,宽体电池包两侧直接装配在门槛梁上;采用贯通式闭口直梁进行Y向传力,并与电池包中间有效连接,极大提升侧碰能量传递和车身结构的稳定性。基于纯电专属平台独有的特性,对安全传力路径进行重新设计。通过“上中下”三条传力路径实现力的分流,快速分散碰撞能量,坚固保护乘员舱安全。
同时由于CTB技术采用全扁平结构的车身一体化设计,两者高度集成,相较于CTP技术,CTB技术下电池能量密度、体积利用率均实现显著提升,对提升续航里程带来实质性赋能。海豹车型作为全球首款搭载量产CTB技术的车型,在电池安全、整车安全、电池容量上有了大幅提升。
3)高扭转刚度媲美百万级豪车,操控与舒适“双能”:
扭转刚度数与整车操控性和舒适性成正比,扭转刚度越大,在弯道行驶时,整车后轴跟随越快,甩尾越小,车辆操控性越好;扭转刚度越大,在过减速带时,产生的形变越小,车辆舒适性越好。
在CTB技术加持下,刀片电池包与车身集成后,宽包电池作为刚性体结构件加强了车身环形结构,同时优化电池包边框结构设计,电池上盖、电芯和边框参与整车传力,进一步加固底盘结构,平衡整车重心,使整车强度大幅提高,整车扭转刚度达40000+N.m/°,媲美百万级豪华旗舰车型。高扭转刚度带来的舒适性与整车操控稳定性,远超同级别车型,轻松应对各种工况与驾驶需求,快速响应。海豹车型麋鹿测试通过车速达83.5km/h,单移线测试通过车速133km/h,最大横向稳定加速度1.05g,同时借助车身结构的优化带来了更高的轻量化系数,达到行业钢车身顶级水平,比肩钢铝车身。
4)超能密封,无惧全工况全天候的严苛考验
CTB技术通过对车身电池密封面的创新设计:将密封面集成为一个零件,大幅提升密封精度,明显改善密封效果;同时针对密封效果进行了多达21种工况下的严苛测试,共历时5000小时,行程超100万公里,完美验证CTB结构下的强大密封效果。
5)CTB技术定义下一代动力电池系统技术路线
在纯电动汽车发展的过程中,电池与车身的关系一直是工程师探索的问题。从直接在燃油汽车上加装电池,到电池包扁平化设计,再到专为纯电动汽车设计的平台,动力电池技术一直在不断发展。高集成化、高能量密度是纯电平台的发展趋势。CTB技术将底盘与电池高度集成,为智能底盘技术打下坚实基础,为实现高阶智能驾驶提供可能。
基于以上思路开发的e平台3.0,具有智能、高效、安全、美学的核心优势,集比亚迪多年电动汽车研发经验的之大成,承载着比亚迪对下一代智能电动汽车的认知与革新。世界正处于百年未有之大变局,比亚迪的创新之路也永不止步。