2.78秒零到百公里加速、CLTC续航800km、19分钟快充、空气悬架、激光雷达、城市NOA、压铸车身技术。不到30万元就能拥有一辆集性能、科技、智能于一身等纯电C级轿车,这——就是小米SU7。
对于这样的配置,SU7到底是怎么生产出来的?又是如何保障产品的质量?带着以上疑问,我们来到了小米超级汽车工厂,探秘工程奇迹背后的故事。
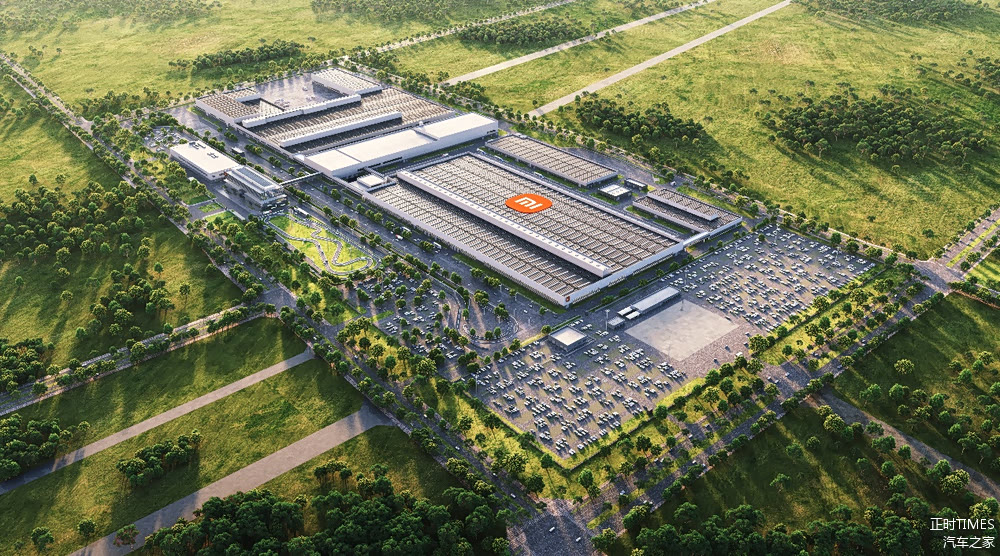
小米超级汽车工厂位于北京市西南角的亦庄经济技术开发区,占地面积达71.8万㎡,工厂内建筑面积达39.6万㎡,可以和2.6个故宫大小相媲美。
顶着小米LOGO的巨大建筑,就是 小米SU7的诞生地,在这片建筑里,按照功能划分为了6个生产车间,分别是压铸车间、冲压车间、车身车间、涂装车间、总装车间以及电池车间。
作为超级工厂,小米汽车将环境建设、环保设施的搭建放在首位。在厂区建筑房顶上,几乎铺满了光伏面板——一个16.2MW的分布式光伏电站,每年可发电1640万千瓦,每年能够减少二氧化碳排放量9905吨,相当于种植了54万颗树。同时,厂区内产生的废水和废气排放,都低于极为严苛的首都排放标准。
其它硬件设施方面,厂区内配套了29个实验室以及一条长达2.5km、涵盖18种测试路况的专业跑道,用于交付前的动态测试验证。
此外,小米汽车还将一个涵盖销售、体验、技术展示、交付为一体的旗舰级综合门店安置在工厂内,消费者可以免费来此参观、体验,也可以在此将下线的新车直接开走。
绿色、环保的厂区环境
进入厂区后,首站是开放给员工和访客的停车场,给人最大感受就是干净、整洁,且没有裸露的地面,全部被绿色植被覆盖,绿树丛阴,环境氛围感整洁拉满。
同时,绝大部分停车位后方都布置了小米的7kW交流充电桩,方便为车辆补能。这种小功率慢充桩尤其适合布置在工作单位和家里,不仅安装便捷,占地面积小,还对电网负担小,对电池也更友好。按20kWh/100km的电耗计算,补能6小时,就能补充超过200km的续航里程。
走出停车场步行3分钟,便能到达摆渡车站,厂区内采用纯电摆渡小车,访客和员工可以便利的抵达厂区任何角落,非常人性化的设置。
位于厂区内的测试跑道及测试车辆
参观首站,就是位于超级工厂的小米汽车旗舰门店。门店占地面积6500㎡。相比普通的小米汽车展厅,这里除了整车陈列外,还有更多技术上的展示和讲解。
工作人员介绍说:小米整车的平台称为摩德纳智能架构,包括小米超级电机、CTB一体化电池技术、超级大压铸、小米Pilot以及小米智能座舱,是小米全栈正向自研生态造车架构平台。
为了让到访用户更直观的看到SU7不同配置车型上电机的区别,小米汽车分别将HyperEngineV8s、HyperEngineV6/V6s进行陈列展示。
在技术方面,V8s电机采用双向全油冷散热、槽满率高达77%的扁线绕组、0.35mm转子超强硅钢片等多项创新技术,最高转速高达27200rpm,能提供425kW功率以及600Nm的扭矩输出。而近日刚刚发布的SU7 Ultra原型车,就采用了后轴双V8s电机,加上前轴电机,整车马力超过1500匹,0-300km/h 加速15.07秒,最高时速超过350km/h。
关于电池,工作人员表示:SU7电池组提供了400V和800V两个平台电压等级,分别对应入门的标准版/PRO和MAX版本。其中MAX版搭载宁德时代麒麟电池,采用871V超高压平台,15分钟就能补充510km的续航里程。此外,电池组还通过CTB技术,将电池和底盘一体化集成,实现了更小的垂直空间占用,让成员仓的空间更大。
安全方面,在压铸车身和电池包的配合下,小米SU7的整车扭转刚度达到51000N·m/deg,带来更好的性能表现。
作为小米生态战略的重要一环,SU7可以与米家生态无缝连接。当驾驶员驾车离家,离家模式将自动激活,家中的各类电器关闭,同时清洁机器人启动,将室内打扫干净,实现了智能化的生活居住。
超700台机器人 走进高度自动化工厂
虽然当天室外环境温度又热又闷,但生产车间里的温度湿度却非常舒适。一方面是为生产人员提供舒适的环境,另一方面,合适的温湿度环境更有助于产品质量的提升,而硬件设施的加持,也让小米超级汽车工厂拥有每76秒下线一辆新车的能力。
车间内参观的首站就是小米赫赫有名的9100吨大压铸机,这里布置了小米全栈自研的一体化大压铸设备集群,整个压铸岛占地面积 840平方米,约有两个篮球场大小,单个压铸机的重量达到718吨,总重1050吨。
作为亮点之一,小米的压铸机具备9100吨的锁模能力,小米的泰坦合金在700℃高温炉熔化为液态铝,然后液态铝通过340倍标准大气压的压力,以25倍的重力加速度,在100毫秒内注入到模具内。压铸机对模具内的泰坦合金施加9100吨的压力,使之金属分子更加紧密,大幅提升铸件的强度和刚度。这种工艺,可以简单理解为高压铸造加锻造的生产工艺。
相比于传统造车工艺,小米汽车通过引入压铸件,改进了传统冲压焊接的制造方法,避免了由于零件多且复杂造成的人力、时间成本浪费。在9100吨压铸机内,可以将72个零件融合在一起,相比传统焊接工艺,焊点减少840个,减重17%,使得生产用时减少了近一半,还有效提升了整车性能。
据介绍,小米的压铸车间每2分钟可生产一个压铸件,泰坦合金还加入了30%的循环铝,每个零件可实现碳减排352.53kg。
此前有研究报告指出,压铸件一旦损坏,存在维修费用高、难度大等问题,小米SU7也考虑到了这点,压铸后地板设置了两层独立溃缩区,可按需更换,专门应对低速和中高速冲击,能尽可能避免伤及压铸件,减少用户损失。
传统铸件生产过程中,可能会产生裂纹、冷隔、摩擦烧蚀等缺陷。为了避免不合格的铸件上车,工作人员表示,在压铸车间内的质检机器人会对每个压铸件拍摄28张X光片,通过自研的X-Eye智能质检系统识别。
值得一提的是,质检还引入了AI质检技术,代替人眼识别缺陷,大幅提升质检效率,准确率>99.9%。在检测过程中,若发现存在残次、不合格的零部件,将会统一存放在“残次区”,等待回收利用。