过去购车时,我们关注的焦点往往聚焦于“这款车的发动机会否遭遇烧机油的困扰?”。然而,近年来,消费者的顾虑日益深化,除了继续关心烧机油问题外,一个新的疑虑悄然浮现——“我心仪的车型是否可能面临机油异常增多的现象?”这一变化,无疑反映了汽车市场对品质与性能要求的持续提升。
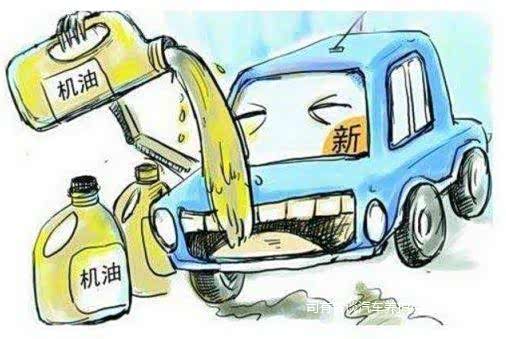
烧机油现象,大家应该都很好理解,烧机油主要源自几方面的原因:
- 活塞环的损坏或缸套的磨损会扩大间隙,使得机油能轻易通过活塞环窜入燃烧室。
- 气门油封一旦损坏,便无法有效密封,导致机油从气门窜入燃烧室。
- 原厂油气分离器若效果不佳,将无法彻底分离机油与气体。在曲轴箱强制通风系统中,机油可能随气体进入进气管。特别是油气分离器设计不当或车辆频繁短途行驶时,油气分离不彻底,带有机油的混合气体会进入气缸燃烧,从而引发“烧机油”现象,显著增加机油消耗量,并导致排气管冒烟和发动机积碳等问题。
处理发动机烧机油问题的常规流程通常始于废气阀的检查与更换,然而,这往往并不能显著缓解烧机油的现象。随后,人们可能会尝试更换涡轮、气门油封等部件,尽管投入不菲,但问题仍可能持续存在。在这种情境下,更换活塞环似乎成为了一种“万金油”式的解决方案,但需注意,并非所有车型都配备有改进型油封和活塞环,因此决策需根据具体车型而定。对于大多数车辆而言,直接更换活塞环并非首选,因为活塞环问题往往源于老化,而这通常是可以通过修复来解决的,毕竟橡胶材质具有可修复性。
此外,见到蓝烟就急于更换油封的做法并不理智。蓝烟并非油封老化的唯一标志,且某些情况下,如早晨启动时的短暂蓝烟,可能并非由油封问题引起。因此,面对蓝烟现象,应保持冷静,综合考量各种因素,避免盲目更换部件。重要的是要认识到,即便油封确实老化,它也不太可能是导致严重烧机油现象的唯一或主要因素。烧机油问题的根源往往更为复杂,可能涉及多个部件和系统的综合作用。因此,在处理此类问题时,应采取全面而细致的诊断方法,以确保准确找到问题所在,并采取相应的修复措施。
对于因活塞环堵塞而引发的严重烧机油问题,一种可行的治理方式是采用如司有普等品牌的行驶中解决方案。然而,必须强调的是,在采取任何措施时,都应避免使用可能损害发动机的泡缸盘轴或长时间怠速的方法,除非所使用的药液已明确标注为安全无害。否则,这些方法可能会损坏凸轮轴、大小瓦、曲轴以及气门油封等关键部件,最终导致发动机需要大修。
相比之下,行驶中能够安全加入油箱或机油的解决方案则是一种更为稳妥的选择。这种方法不仅符合我们一贯提倡的“以养代修”理念,即通过日常保养来预防和减少故障的发生,同时也避免了不必要的拆解和潜在的风险。因此,在面对烧机油问题时,我们应该优先考虑这种既安全又有效的解决方案。
烧机油现象虽易于理解,但机油增多现象却往往令人困惑。实际上,增多的机油并非由发动机自行产生,而是源于为发动机提供动力的汽油。在发动机运作过程中,由于活塞环与气缸壁之间并非完全密封,存在微小间隙,这导致机油有可能从活塞环窜入气缸,同时,气缸内的部分燃油蒸汽和未充分燃烧的汽油也可能通过这一间隙进入曲轴箱。因此,随着时间的推移,机油中会逐渐混入这些额外的汽油成分,从而呈现出机油增多的现象。
具体而言,活塞与气缸壁之间的密封依赖于活塞环的紧密配合。然而,为了满足安装需求,活塞环与活塞之间必须保留一定的余量,这就不可避免地在活塞环与气缸壁之间形成了一定的“空间”。在发动机高速运转时,这些微小的间隙便成为了汽油蒸汽和未燃汽油进入曲轴箱的通道。随着这些汽油成分的积累,机油量便会逐渐增加。
在发动机运行过程中,汽油与气缸壁上的油膜混合后,由于难以气化,特别是在冷车阶段,其燃烧效率更低。这种混合物中,一部分被活塞环刮入曲轴箱内,而另一部分则可能逐渐堵塞活塞环的气环,影响其密封性。这种现象在直喷发动机及短途行驶频繁的车辆上更为常见,因为直喷发动机喷油量较大,且短途行驶时发动机未达到最佳工作温度,油膜和汽油混合物的气化与燃烧均不充分。
在中国东北等寒冷地区,冬季用车时,由于环境温度低,热车时间延长,冷车状态下喷油量显著增加,进一步加剧了燃油进入曲轴箱的情况。这一现象并非孤立,而是全球汽车行业共同面临的挑战,SAE(国际自动机工程师学会)的技术文库中就有大量相关案例记载。
我们在协助整车厂进行直喷发动机验证实验时,也频繁观察到机油增多的现象,尤其是在模拟冷车启动和频繁启停的实验条件下,机油增多尤为显著。这表明,机油增多问题是一个复杂且普遍存在的技术问题,需要汽车行业持续关注和深入研究,以寻求更为有效的解决方案。
总的来说,参与燃烧的汽油混进机油里,导致机油总量增多,大多由于以下两种原因:
1.汽油雾化不充分,紧贴在汽缸壁上流入曲轴箱内;
2.进入曲轴箱的汽油无法被及时回收。
以上两点其实在许多厂家产品中都存在的问题,别以为只有机油增多的情况下,才说明汽油混进了机油里面,实际上就算机油量没有增加,机油也很可能已经被汽油窜得变质了;因此不仅仅北方地区汽油窜进机油的现象比较普遍的。南方所处的相对炎热的天气汽油也很爱窜门到机油里面,影响机油的品质。只是在南方受气温的影响,机油增多速度远不如北方来得快。
对于烧机油与机油增多现象,可以简化为一种动态平衡的理解:在发动机运行过程中,机油的消耗与增多往往并存且相互影响。当机油的消耗量与增多的量保持在一个相对稳定的水平时,机油总量能够基本维持不变。然而,当机油的消耗量显著低于其增多的量时,就会出现如本田发动机所经历的机油异常增多现象。
针对机油增多问题,汽车制造商们普遍采取了两大解决策略:一是从源头上减少汽油窜入机油的量,通过优化发动机设计、提升活塞环与气缸壁的密封性能等方式,来降低汽油蒸汽和未燃汽油进入曲轴箱的比例;二是增强机油中汽油的蒸发能力,使这些汽油能够更高效地返回燃烧室进行燃烧,从而减少机油中的汽油含量。这两种策略共同作用于机油增多问题,旨在恢复机油总量的平衡状态。
在寒冷地区机油增多现象更普遍存在的直接原因就是气温过低,发动机升温慢,影响了汽油的及时正常蒸发。所以在发动机设计时,就应充分考虑如何令发动机曲轴箱快速升温以保证正常的汽油蒸发这一问题。令发动机快速升温,厂商可以从多方面着手,包括ECU软件的优化、合理设计的空调控制单元、TCU软件的优化、合理设计的散热器下水管等。
1、通过ECU软件调整燃油喷射
上面提到,过量的雾化不完全的汽油被喷油嘴从侧面喷射到缸壁上,产生了缸壁的"湿壁"现象,汽油融化了缸壁上的油膜,在活塞的作用下慢慢地与机油一起渗进曲轴箱,时间长了之后最终导致机油增多。
汽车厂商当然也认识到这一点,针对汽油沿气缸壁进入曲轴箱的问题,厂商可以通过升级发动机的ECU软件,优化燃油喷射和点火时机,提高燃油喷射压力,使直接喷射到气缸内的汽油雾化效果更好,使汽油不在气缸壁上形成留存,大幅减少燃油"窜入"机油的可能性。同时,高压喷射出较小的汽油液滴与空气混合后能更充分地燃烧。配合燃油喷射和点火时机的优化,使汽油得到更充分的燃烧。
2、空调控制单元的合理设计
为了让曲轴箱里的汽油快速挥发,汽车厂商可以使用全新设计的空调控制单元,让本来流向空调的热量暂时先供向曲轴箱,让曲轴箱快速升温。当曲轴箱达到汽油蒸发温度后,热量才开始供向空调。一般来说,这个过程不会被设计得太长,一般为3分钟左右,对空调的升温、排放和噪音并没有多大影响。
3、TCU软件的优化设计
为了让混入曲轴箱的汽油快速蒸发,合理设计的TCU(温度控制单元)软件就显得十分重要了。在汽车冷车刚启动时,为了使发动机快速升温,加速蒸发机油里窜入的汽油,TCU软件会适当调高发动机转速,使曲轴箱尽快达到汽油蒸发温度,这在冬天与及寒冷的北方地区尤其重要。当曲轴箱温度足够后,TCU会逐渐调低发动机转速至正常水平。因汽油的蒸发温度较低,TCU控制的转速提升时间较短,对油耗、噪音和排放并没有明显的影响。
其实在许多新车型上,为了使三元催化器快速升温达到工作温度以减少环境污染。
4、散热器下水管的合理设计
为了让混入曲轴箱里的汽油能够快速蒸发,汽车厂商可以把原来始终联通发动机和变速箱(CVT无级变速箱)散热器用一个可控的节温器进行分隔。低温启动时热量锁暄在发动机内,迅速加热曲轴箱让汽油蒸发;当需要散热时打开节温器,CVT散热器和冷却水箱一起帮助发动机散热。如此设计的散热器下水管不仅提高了机油中汽油的蒸发量,而且对动力系统的冷却没有丝毫负面影响。
上述几种都是汽车厂商应对发动机机油增多的对策,可以看出除了第一个措施通过ECU程序调整燃油喷射压力和点火时机之外,其它三个措施的目的都是为了使曲轴箱快速升温,使窜进机油里的汽油能尽快达到蒸发条件。
机油增多现象并非某一品牌的特有问题,而是广泛存在于多个合资品牌与自主品牌中,尤其在寒冷的北方地区,这一现象更为显著。随着对机油增多原因的深入了解,我们认识到这主要源于发动机工作过程中的物理现象。
面对这一问题,汽车制造商们已经积极采取行动,不仅提供了延长保修期、免费更换发动机总成等解决方案,还承诺了终身包修政策,这充分显示了厂家对消费者负责任的态度。值得欣慰的是,截至目前,尚未有因机油增多直接导致发动机损坏的案例被证实,这进一步减轻了消费者的担忧。
因此,对于广大车主而言,在享受新技术带来的高效燃油经济性时,只需遵循厂家手册的指导,定期进行车辆保养,并在日常使用中多加留意、勤加检查,便能有效管理机油状况。无论是机油增多还是机油消耗较大的情况,其实并没有我们想象中的那么可怕,关键在于我们如何正确应对和妥善处理。