摘 要:目前汽车轻量化被公认为是实现降低油耗和气体排放量最直接有效的方法,已成为行业共识,并成为世界各国的汽车生产制造商创新技术的研究热点。本文为了分析汽车生产用铝合金的点焊工艺参数与过程和性能的情况,通过对影响 5083 铝合金材料的电阻点焊接头的各种因素进行了相应试验,从而找出影响铝合金点焊时接头质量稳定性的因素及工艺缺陷,为铝合金在汽车上的应用提供了质量保证。
关键词:汽车轻量化;铝合金;点焊;接头;性能分析
1 课题背景及意义
在现代汽车工业生产中,实现汽车轻量化的途径主要有三个方向:(1)采用新型的轻量化材料;(2)优化设计汽车的结构和形状;(3)应用先进的加工技术,其中铝合金突出的性能和优势使其成为汽车轻量化的首选材料。
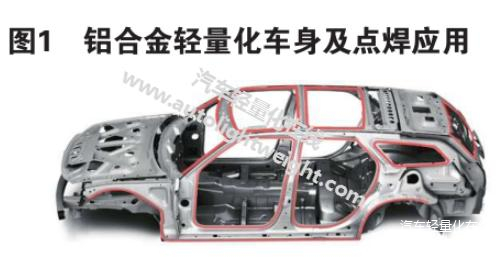
点焊在汽车用焊接技术中是主要的方法,可算是汽车生产中的主要焊接工艺。这种方法不仅质量可靠,效率高同时还容易利用大量机器人来进行焊接。但是,由于铝合金材料与碳钢材料的不同,使得铝合金点焊在汽车制造中的运用受到了限制。据了解目前铝合金汽车单独采用电阻点焊的不多,基本采用气保焊,激光焊,等连接工艺。
2 铝合金点焊所存在的问题及现状研究
2.1 所存在的问题
2.1.1 铝合金点焊焊点质量不稳定的四
个方面
喷溅与飞溅严重。如图2所示熔核
喷溅和表面飞溅。
(2)焊点表面质量不好;(3)熔核内
部易产生缺陷;(4)熔核尺寸变化大。
2.1.2 电极严重烧损,寿命变短由于铝合金点焊时电极的严重烧损,导致65寿命很短,如图3所示。
电极烧损根本原因就是电极表面铜铝合金化反应,而反应时间对合金化反应程度的影响又很大;合金化反应的条件一是成分二是温度。
2.1.3 没有可靠的焊接质量控制手段
铝合金点焊的质量问题要比低碳钢复杂得多,主要是铝合金材料的电阻率低,阻温系数也较小。因此点焊低碳钢时保证质量的各种手段并不适合铝合金材料,特别是焊点表面成形质量差和工件电极的粘连问题更是没有好的办法。
2.2 问题的研究
随着铝合金材料的广泛应用,很多专家做了大量的研究工作,具体如下所述:
(1)通过把铝合金点焊的焊接性能和电极寿命试验,提出:为了加速熔核形成,在铝合金的两面镀不同厚度的铬酸盐层,使它与电极的接触电阻相对较小,不但保证了接头的性能,还提高电极的使用寿命。
(2)通过点焊熔核孕育处理理论与方法的研究结果表明,孕育处理不仅提高点焊接头力学性能,特别是疲劳强度。对点焊的质量控制问题提供了有效的理论基础和依据。
(3)用数值模拟法模拟铝合金点焊过程的热—电—力学过程,分析电极头与铝板接触上的瞬时温度分布,得出熔核尺寸及接触面积随时间的变化规律、电极表面压力及温度的变化规律以及焊接区的等效塑性应变及残余应力分布,并预测点焊熔核的生长、电极磨损和裂纹形成情况等。
3 本文要研究的内容和方案如下
随着铝合金在汽车生产中的广泛应用,研究铝合金点焊工艺问题是为了生产运中可靠应用的基础和关键,根据目前大多铝合金电阻点焊领域科学研究的结果,确定了本文的研究目的,方法和内容。
本文在同行业专家研究的基础上,为了提高铝合金点焊的接头强度,使用金属电极带辅助点焊改变焊接区的温度场从而改善焊接接头表面的接头质量。分析了铝合金电阻点焊的特点,设计了不同工艺参数对铝合金点焊质量的影响,进行试验和分析,从而获得最佳焊接工艺参数,完成铝合金电阻点焊的焊接工艺设计。 为了能更确切地解决铝合金焊接性问题,我们认为与碳钢点焊工艺对比,研究焊接参数及改变温度场对于铝合金点焊接头的质量和性能的影响更有意义。
4 铝合金点焊试验设计方案及其分析结果
4.1 实验材料与采用的设备
4.1.1 实验材料
试验所采用铝合金材料为厚度为1.5mm的5083铝合金。其所含的化学成分见下表1:
4.1.2 试验设备
本项目焊接设备为奥地利福尼斯公司生产的固定式C300Delta电阻点焊机,图4为点焊机外观与电极形貌。
4.2 试验的方法
铝合金电阻点焊接头常温抗剪试验按照GB/T 2651-1989标准制备,试样加工成100mm×25mm×1.5mm的尺寸,点焊接头采用搭接形式。焊接试验前,铝合金试样表面首先利用角磨机打磨以去除表面的氧化膜,然后在酒精中进行清洗去除杂质。本研究通过对焊点熔核尺寸大小和焊点表面压痕深度的测量和分析,来选出合适于试验铝合金板的点焊参数范围,从而进行铝合金板的点焊工艺参数优化试。之后再对点焊接头进行金相分析,拉伸试验来检验和选取工艺参数的范围。
4.3 实验的参数
点焊工艺参数的选择主要根据金属材料自身的性质、板料厚度和点焊设备的特点。本试验用的Delta直流电阻点焊机,主要的参数有:焊接电流、焊接时间、电极压力等。通过对试验的结果进行分析后,明确了对熔核质量影响最大的参数是焊接电流,因此该实验选取了该厚度板,采用搭接接头的5组工艺参数如下表2所示。
4.4 试验结果
4.4.1 试件宏观照片如图5
从试件的焊接过程和宏观形貌中可见,在合适的焊接参数下,可保证焊接铝合金的过程无飞溅,提高了焊接质量,减少了能量损失。
4.4.2 试件熔核外观形貌,如图6
4.4.3 试件拉剪力
试件进行拉剪试验,拉剪力在电流为21KA时,达到最好,此时熔核直径也较大。大量实验研究表明,焊接接头强度与熔核直径成正比,熔核尺寸的增加,使接头拉剪力也随之增加,随着电流增大时,焊件加热增快,但焊接电流过大时加热程度过大,熔核扩展的速度会超过塑性环扩展的速度,这样就会导致熔核内部的液态金属在电极压力作用下挤出焊接区域而形成飞溅,使形成的焊点强度有所降低,焊件的拉剪力也会随之下降。
4.4.4 破坏形式(图7)
对焊件进行破坏性试验,焊件呈纽扣断裂形式,说明两个试件已经完全熔合。
4.4.5 电极形貌
由于点焊过程中使用的Delta带极电阻点焊机,本设备特有金属工艺带既能保证焊接时提供足够的热输入,又能对电极与焊点起到保护作用,图8,9对比了在使用电极工艺带后电极形貌的对比,传统点焊对于铝合金焊接几十点后就需要处理电极,而Delta带极电阻点焊焊接过程中在参数合理的情况下,几乎实现了零飞溅,不仅节省了电能,而且充分保证了焊接质量,提高了焊接效率,为铝合金点焊能够在汽车行业中使用提供了可靠保障。
5 实验结果分析
(1)通过Delta带极电阻点焊机可以完成铝合金薄板焊接,各项性能基本满足要求,焊接质量良好。
(2)大量实验数据分析表明,焊接过程中的主要影响参数为焊接电流,当焊接电流为20-21KA时,可获得较好的熔核直径和拉剪力。
(3)通过Delta带极电阻点焊机的使用,既能保证焊接时提供足够的热输入,增加了电极使用寿命,对焊点起到保护作用,同时提高了生产效率。
(4)本文在重点研究了焊接电流对焊接过程中的影响,基本可以保证汽车用薄板铝合金的焊接质量,为了提高焊接工艺,后续拟定对焊接时间,焊接压力等参数进行进一步分析,逐步完善薄板铝合金的点焊工艺。
来源:期刊-制造与工艺
作者:穆春艳、王蕾
单位:长春汽车工业高等专科学校