福伊特复合材料公司采用了新方法,实现CFRP(碳纤维复合材料)车身包裹架(rear wall)在全自动模块化生产线上进行批量生产,这些新方法包括一种新的纯数字化开发成型工艺,福伊特粗纱涂敷器和Ultra-RTM工艺。这种碳纤维复合材料零件一般在豪华型乘用车上有所应用。
1.提升预制效率
虽然由纤维复合材料制成的高性能部件很轻,但它们的成本明显高于由钢或铝制成的部件。而对于碳纤维车身包裹架,汽车制造商对其供应商的期望是轻质、具有高扭转刚度,且价格合理。
预成型产生的费用高达CFRP组件成本的一半,这一事实促使福伊特复合材料公司努力在这一领域进行技术革新,以改变这种现状。位于Garching(德国)的该公司尝试了一个新的方向,开发了先进的工艺:新的纯数字化开发成型工艺,福伊特粗纱涂敷器和Ultra-RTM工艺。在紧密相连的工艺中生产高弹性轻质部件,主要半成品(碳纤维粗纱)产生约30%的车辆扭转刚度,而且所有重量仅为其前身的一半。
2.覆盖过程的模拟
福伊特团队完全使用模拟方法设计了成形过程和相应的工具。碳粗纱的特定材料轮廓在专用试验台上进行校准和验证。首先,模拟使得能够对成形过程做出基于事实的决定,并且展示出了使用分段冲压工具的预成形如何优于使用双隔膜的方法。模拟一直到粗纱水平,二维堆叠的悬垂模拟保证了高质量的成形。机器和工具立即可用于大规模生产,无需任何测试或后续修改。
3.专门开发的模拟环境
市场上可买到的模拟系统都没有为福伊特复合材料提供覆盖模拟所需的功能范围。这就是为什么内部可用的设计工具的范围扩展到包括使用内部开发的例程的合适的模拟方法和经验证的材料轮廓,如图1。它们被设计成适用于缝合和未缝合的纤维,以及树脂浸渍或干燥的纤维和用粘合剂处理过的纤维。
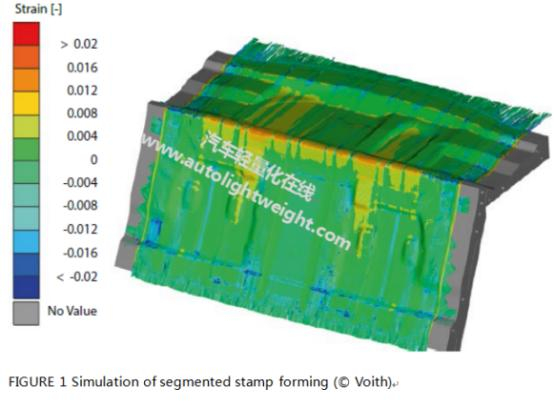
采用一种新的各向异性材料法评估的半成品纺织产品的材料和接触行为。这种特殊的方法将每个单独的纤维层完全建模到其粗纱水平,展示了不同层之间的相互作用。该过程的结果是一个以面向功能的体系结构为特征的组件模型。可以在预先几何优化中检测诸如皱纹,起伏和间隙的属性。
尽管堆叠结构复杂,但即使在高分辨率的亚粗纱水平上指定元件尺寸,也很少超过10小时的计算时间。鉴于这种短的计算时间,说明各种过程概念和参数的同时虚拟测试和量化是合理的。
4.用粗纱施加器直接铺设纤维
CFRP车身包裹架的二维堆栈由生产线的核心技术-专利的福伊特粗纱涂抹器(VRA)生产。由粗纱和粘合剂在线生产的胶带可以全自动堆叠。因此,VRA构建了复杂的层结构。其设计特别符合相应组件的要求--无需使用任何成本密集型半成品。
旋转台为VRA提供了将纤维放置到所需角度所需的灵活性。这就形成了一个复杂的预制件,带有局部加固点,其壁厚范围为1.5到3.7mm,如图2所示。碳纤维精确地放置在所需的位置,以最大限度地减少材料消耗。VRA具有多达19个纤维层,特别强化了后来必须承受高度集中载荷的区域,如图3所示。
福伊特涂覆器的主要优势包括:
Ø 由最具有成本效益的粗纱和粘合剂原料制成的预制件
Ø 模块化系统概念允许同时生产多个纤维带
Ø 纤维切成一定的长度
Ø 纤维可以直接放置在任何所需的角度
Ø 可以沿最终轮廓的层结构堆叠,最大限度地减少了浪费
Ø 线性驱动技术确保快速,稳健的操作组件设计,提供充足的自由度
Ø 在线浸渍或粘合剂应用作为生产过程的一部分,以及质量保证。
5.有针对性地控制摩擦行为
福伊特复合材料公司未来的目标是通过有针对性地使用工艺参数来控制摩擦系数。换句话说,纤维的方向、与活性粉末粘合剂的相互作用以及成形温度和压力应该与应用精确对准。在不同的工艺环境中测试了不同的粘合剂应用组合。 测量的系数值介于0.25和1.7之间。值得注意的是,松散粉末表现出比预烧结涂层更低的摩擦系数。
6.综合生产流程
每周都有数百个可组装的复合材料车身包裹架离开福伊特复合材料工厂。在它们的全自动生产线上生产,每个子流程至少使用一项创新。VRA首先从粗纱中平行生产四条胶带,然后再喷上一层活性环氧粉末粘合剂。在多个辊子的张力下运输固定胶带之前红外辐射短暂地预先烧结涂层。在将干胶带切割成一定长度后,VRA会在确定最终轮廓之后紧密地将它们构建成二维堆叠。在特定的机械值方面,例如织造或分层纤维,与载荷方向精确对准的带子明显优于传统的半成品材料。
二维纤维板的最终3-D版本通过顺序印模形成。该方法的优点在于上部工具适应施加到不同厚度的部件的不同区域的压力。然后,超声刀在进行Ultra-RTM过程之前切割预成型件。
这种新的RTM工艺以相对较低的压力工作,其中粘合剂颗粒执行两个关键功能:将纤维固定在适当位置,同时还形成微通道,通过该微通道将树脂引入复杂的包裹架预制件结构中。
Ultra-RTM显着优于高级RTM流程(advanced RTM),同时需要更少的资源。液压机也设计得相应地更小并且循环次数增加。
然后使用高速铣削为车身包裹架提供最终几何形状。在最终的生产过程中,金属附件在完全自动连接过程中通过胶合或铆接到位,如图4所示。
7.富有成效的智能工厂
在配备广泛的传感器的情况下,四个生产线的各个系统模块和机器人可以提供连续的过程数据,组件本身也是如此。它们构成了网络化生产的基础。智能链接时,它们还可以实时了解每个系统模块和组件的生产状态和状态。这确保了,例如,总是可获得足够的材料、只有所需质量的产品离开工厂;例如超声刀在适当的时间被清洁并且机器具有足够的消耗品供应。
OPC-UA接口为质量控制提供重要的关键性能指标(KPI),关键是每条生产线的效率和整个CFRP车身包裹架生产的整体效率(整体设备效率,OEE)。如果所有生产站点相互连接,则数据提供识别过程和影响因素之间的全局关系的机会。适当的措施改善了产品和制造过程的生产率。
8.总结
CFRP车身包裹架是在模块化和全自动生产线上批量生产的。每年为汽车组装生产多达65,000个这些高性能组件,见图6。其中的各个生产步骤紧密相关。基于粗纱和粉末粘合剂,该工艺消除了昂贵的半成品的使用。VRA智能直接纤维放置显着降低了材料消耗。纯数字化开发的成型工艺和工具也有益于环境。并且由于精确模拟,设计不需要使用通常需要的测试运行的资源。
作者:DR.-ING. LARS HERBECK;DR.-ING. JAROMIR UFER;ANNA POINTNER, M. SC. 轻量化在线翻译整理