本特勒(Benteler)与帕德博恩大学(Paderborn University)合作开发了一种由金属和塑料制成的混合式前支架。并依靠粘合剂进行熔合连接。除了减轻重量之外,这一设计的优势在于可以集成其他功能,例如充当车身底板,改进空气动力学或BEV的充电技术。
01 底盘应用中的混合材料设计
目前,大多数汽车支架都使用了由钢板制成的传统壳体结构。这些结构存在着巨大的轻量化潜力来减少燃料消耗以及车辆的二氧化碳排放。这就是为什么汽车零部件供应商本特勒汽车公司与帕德博恩大学以及纤维增强塑料(FRP)供应商一起开发了轻型混合材料副车架。
底盘技术中的混合材料解决方案在大批量生产中并未普及。 目前占主导地位的钢结构确实具有成本效益,但同时也表现出了更高的重量。 铝结构总体上更轻,但成本较高。 即使完全由纤维增强塑料制成的结构也比钢更昂贵,尤其是碳纤维增强塑料(CFRP)。由于有限的稳定性,更具成本效益的玻璃纤维增强塑料(GFRP)不适合单独用于副车架。 然而,FRP具有许多优点 - 例如,成形的高度设计灵活性。 它们将诸如金属板成形的特性与铸造材料的特性结合在一种材料或部件中。 通过这种方式,可以在单个工艺步骤中制造高度复杂的结构。
由不同的材料组成的混合结构解决了经济(低成本)和技术(低重量)要求之间的权衡。 与传统结构相比,多材料系统由于最佳可能的材料组合而提供高轻量化设计潜力。
钢结构的副车架作为这种轻量化设计解决方案的对照模型。 该参考模型由Benteler开发并大规模生产。 与此同时,通过铝铸造得到另一种支架。 这种支架质量较轻,但价格更高。 这就是为什么它被用于高档汽车的原因。 因此,塑料或混合材料解决方案代表了一种附加选择,具有该应用的巨大潜力。
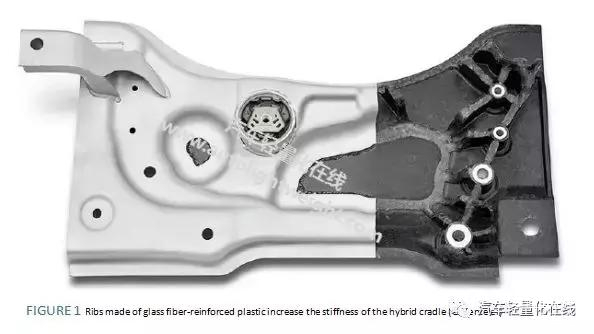
02 概念设计
所选择的概念设计包括一个外壳,上部外壳由金属制成,下部外壳由FRP制成,如图1所示。混合材料副车架的结构源于该概念的进一步发展。它是由一个铝板上壳与一个压缩成型的由玻璃纤维增强塑料制成的下壳和加强筋连接而成。铝上壳的生产采用了传统的成形工艺和连接工艺。来自EN AW 5xxx系的材料用作原材料。这些材料具有良好的拉伸和成型性能,对腐蚀的敏感性较低。所有连接点(如白车身、控制臂或转向装置)都安装在金属外壳中。这样,大约70%的负载由金属传递。塑料下壳只简单地承担了加固的功能,如图2所示。
在下壳体中使用了多种类型的FRP。肋条采用具有准各向同性材料。使用价格合理的聚丙烯(PP)作为基体,玻璃作为纤维材料也提供了良好的成本基础。对于基板,使用了一种织物结构,该结构也由嵌在聚丙烯基体中的玻璃纤维制成。这种材料提供较少的成型可能性,但刚性更好。各种半成品的集体加工——在单个冲击挤压过程中堆叠在一起——由于共享的基体,而形成了理想的化合物。
铝合金上壳与FRP下壳的选材组合,使其具有良好的腐蚀性能,这是一个特别适用于底盘的重要标准。在这方面,在下侧使用FRPS是最有意义的,因为PP对污染、化学品、盐和水具有极强的抵抗力。同时,纤维增强聚丙烯和铝热膨胀系数的相对相似性降低了接头处的张力。考虑到这一点,使用特殊的连接工艺将由FRP和铝制成的成品半壳组合在一起。
03 连接技术
混合材料组件的关键是连接技术。 选择的连接技术在混合材料副车架应用方面具有创新性。 因此,必须在样品和组件级别进行广泛的测试。 尽管如此,已建立的标准过程也被用于开发混合材料解决方案。由于聚丙烯是非极性的,因此加入材料变得困难。 胶粘剂粘附力非常弱,这就是为什么这种原料不适合粘合剂粘合的原因。最终通过开发新的连接技术解决了这种冲突:与粘合剂的熔合连接。
必须使用粘合剂。通过这种方式,一方面具有足够的强度,另一方面也能够实现可预测的失效行为,从而实现复合粘结。它在金属上形成一个热塑性层,与金属以及其他塑料都能很好地粘合。融合预先施加的粘合剂为创建最佳混合复合材料奠定了基础,因此也为混合副车架奠定了基础。同时,通过局部有限的FRP成形,可以实现公差补偿。
04 功能整合
混合前支架开发的另一个重点是功能的集成。 该产品的附加价值不仅仅在于通过更换钢/铝副车架(图2)实现的减轻重量,而是功能集成的可能性。 在压缩模塑过程中可以引入附加的功能组件,这在金属结构中是不可再现的。 与参考零件相比,这种方法可以减少生产成本,减少组件数量。
由于车身底板已经由FRP制成,如图3所示,因此可以避免地板下保护的额外成本,并且不需要额外的组装工序。此外,集成的塑料下壳还增强了空气动力学特性,因为可以容易地实现空气偏转结构和扰流板。在冲击挤压过程中,可以直接在FRP材料中形成用于电缆或较小附加部件的紧固元件。
其他功能也可以集成,这使得该产品特别适用于电池电动车(BEV)和插电式混合动力电动车(PHEV)。 在这里,无线充电系统将是未来一个重要的便利因素。对于由金属制成的传统副车架,无线电动车辆充电(WEVC)目前采用感应线圈的形式来解决。 相反,混合前副车架的FRP允许电磁场的传输。 这使得WEVC能够直接集成到FRP下壳中而无需额外的部件或安装件。 铝制上壳已经成为电磁容差屏蔽(EMC屏蔽)。 结果是更好的封装 - 组装,需要更少的步骤,线圈的机械保护得到改善并且成本降低。
此外,FRP具有高度的自阻尼。 玻璃纤维增强塑料车身底板下的功能整合可对底盘的声学特性(结构噪声向白车身的传递)产生积极影响。
05 总结
本文所述底盘技术领域的混合材料方法展示了轻金属和FRP最佳设计的组合。因此,该轻量化设计解决方案在技术上和经济上都是合理的。
此外,功能的集成为减少组件数量提供了多种可能性,从而相应地减少了材料和装配工作。这些措施还带来车辆重量和成本的额外降低。使用副车架为技术试验台所获得的技术方法可以转移到其他底盘部件或类似的汽车应用上。这有可能在广泛的产品范围内进一步降低重量和成本。
来源:作者: MATTHIAS KÖRNER, M. SC
DR. ING. FRANK HÖCKER
ALEXANDER BÖTTCHER, M. SC
汽车轻量化在线翻译整理
特别声明:本文为汽车轻量化在线原创技术文章,版权归汽车轻量化在线所有,未经作者允许禁止转载和改写。如需转载请联系编辑,微信号:qcqlhzx