简 介
宝马2系Active Tourer全新插电混合动力版车型搭载了开创性的动力总成架构,将前轮内燃机驱动与后桥电机驱动相结合。此概念将电力驱动与传统驱动系统的优势进行了融合。借助吉凯恩第二代创新型eAxle, 可以实现多种驾驶模式:纯电动模式适用于本地零排放驾驶;电气全轮驱动模式适用于增强牵引力,增大传动动力;混合动力驱动和增强功能可将引擎扭矩和电动机扭矩相结合。
电动机可提供的最高功率为65kW,最大扭矩为165Nm,最高转速为14000rpm.
经过对eAxle概念的进一步优化,吉凯恩成功推出了第二代eAxle技术。组件经过重新设计后,在安装尺寸没有任何增加的情况下,可传输更大扭矩。
eAxle采用固定的传动比,可向后轮传输2065Nm的输出扭矩。如有需要,电气全轮驱动模式可提供全轮驱动车辆的功能(如优异的牵引力和驾驶性能) ,除此之外,该模式还可通过能量回收给电池充电。此传动系统概念可省去前后桥间的机械连接(传动轴) 。此减少的重量虽只能部分抵消电气化所需组件的额外重量,却完全消除了PTU、传动轴和部分RDU带来的损耗。
为提高效率,通过电子断开差速器(EDD)中集成的离合器,可将电动后桥与传动系统断开。电动或混合动力模式下的最高时速均可达到125km/h ;如要提速,齿轮箱会将电动机与传动系统断开,然后仅由内燃机为汽车提供动力。
基于车辆架构的关键齿轮箱要求
第二代eAxle是吉凯恩已得到市场肯定的eAxle系列的升级产品,并且已经安装在标致3008Hybrid.宝马8、保时捷918 Spyder以及经沃尔沃全新SPA平台制造出来的车辆上,包括XC90和S90
全球对于具有全轮驱动功能且燃料效率得到改进的车辆的需求不断增长。新开发的eAxle装置能够符合这些要求,并且可以帮助汽车制造商达到客户预期,加快其产品的二氧化碳减排。
吉凯恩第二代eAxle技术具有以下关键特征:
单速变速器,可用于电动、混合动力和能量回收驱动模式。
紧凑型偏置设计,可轻松地集成到传统的传动系统结构内。
电子断开差速器(EDD), 可在特定的速度下断开,以最大限度地减少损失NVH和效率均得到优化的齿轮组和轴承布置。
宝马2系PHEV车辆概念
宝马公司在其2系Active Tourer上搭载了这款创新的动力总成架构。这款插电式混合动力车辆将前轮驱动与1.5升3缸内燃机和6速自动变速器相结合,混合动力驱动装置位于后桥。混合动力驱动装置由一台电动机和集成了电子断开差速器(EDD)的吉凯恩第二代eAxle组成。
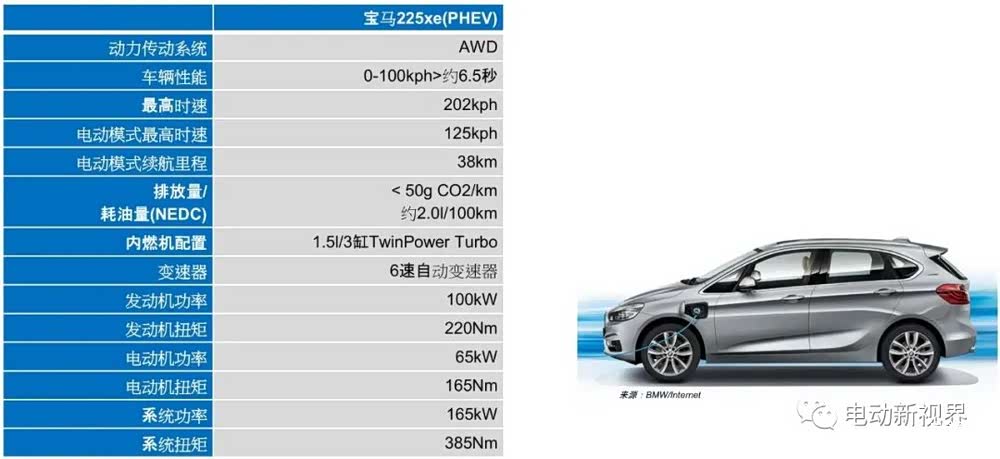
图1:车辆和系统性能一来源:互联网/吉凯恩
宝马225xe的系统总输出功率为165kW,其中100kW由内燃机提供,剩余的65kW来自电动机。平均燃油消耗约为2.0L/100km,相当于NEDC测试中少于50g/km的二氧化碳排放量。最大电动续航里程为38km。
该系列车辆选择动力总成配置(传统内燃机为主驱前桥提供动力,次驱后桥采用电动方式)这种配置在没有机械卡丹轴的情况下可以提供电动全轮驱动(eAWD)功能(见图2) 。
这种“分轴式”混合动力概念将电力驱动的优势融入到那些只采用内燃机的车辆中,如果行驶距离较短,可实现本地零排放,而作为一款全轮驱动车辆时,其传动动力更强。利用后桥的附加电动机,这种动力总成概念可以在制动和减速阶段进行能量回收,从而帮助提高车辆的整体效率。省去前后桥间的机械连接(传动轴)所减少的重量虽然只能部分抵消电气化所需部件的额外重量,却完全消除了PTU、传动轴和部分RDU带来的损耗。这样不仅让驾驶人员能够享受到eAWD车辆的双重优势,而且可以最大限度地减少油耗。
由于混合动力驱动概念由两个单独且相互独立的传动装置组成,因此可将其更容易地集成到全球车辆平台内。此外,可以将电力驱动变速器的机械复杂性和系统控制的复杂性保持在合理且具有成本效益的水平,与此同时还有机会采用模块化方法,即通过电动机安装不同级别的功率。
图2:宝马225xe传动系统架构-来源:互联网/吉凯恩
此传动系统架构可使车辆能够以三个不同驱动模式运行:
纯电动模式(ePower) :车辆最高时速可达125km/h,后轮驱动只由电池和电力传动装置提供动力。
eAWD模式:内燃机和后桥电动机协作实现油耗和驱动性能的完美结合。
前轮驱动模式:动力只由内燃机提供。
图3:宝马225xe的运行模式[1]
后桥E-AXLE驱动的关键性能数据
eAxle可分两个阶段将电动机的高输入速度降至车轮速度,并且能够在此过程增加扭矩,随后直接将扭矩传送至车轮。此驱动装置最高可产生2065Nm的输出矩,并且能够达到65kW的输入功率以及14000rpm的输入电动机转速。该驱动配有一个电子断开设备,这是因为车速超过125km/h时不再需要混合动力驱动。
下表总结了齿轮箱的关键性能数据。
齿轮箱布局和差速技术
齿轮箱规格
整机重量只有20.2kg,长度仅229mm,能够在受限的封装空间内完成包装和安装。该齿轮箱在重量、效率和NVH方面均进行了优化。
图4:吉凯恩第二代eAxle及主要尺寸
齿轮箱布局
宝马2系Active Tourer上搭载的eAxle为单速设计,采用双级齿轮系,固定传动比为12.5作为电动后轮驱动装置的组成部分,该齿轮箱的设计同样可以满足最高的效率和性能要求。
输入轴经由一个套管与电动机输出轴相连,并且将电动机的速度和功率传送至中间轴。中间轴可以降低转速及增加扭矩,并将扭矩传输给与电子断开差速器(EDD)焊接在一起的齿圈。侧轴可以从差速器获得扭矩,并将其传送至车轮。
图5:吉凯恩第二代eAxle剖开立体图模型
在断开模式下, EDD会中断电力牵引马达传给差速器侧轴的扭矩和速度。整个齿轮组会停止转动,以避免旋转齿轮所带来的搅油损失,并支持内燃机驱动车辆时的出众效率性能。在电动模式下,经电磁执行器接合的爪形离合器会将牵引电动机重新连至车辆侧轴。
在最相关驱动条件下所显示的出众效率设为主要开发目标之一。通过在所有传动轴及电子断开差速器(EDD)处布置浮动式滚珠轴承,使得实际效率达到97.5%以上,并将轴承损耗降至绝对最小值。采用减摩密封圈可抑制输入轴的高速,进一步降低不应有的损耗,并且提高效率。
图6:吉凯恩第二代eAxle系统剖视图
为使封装空间得到最佳利用,变速器的设计采用偏置架构,并且不需要连接轴。这种设计方法被视为一种具有成本效益的方法,并且有助于降低整体复杂性。
齿条接口配有一个套管,位于电力牵引马达输出轴与变速器输入轴之间。该设计可以在径向及角向补偿两轴之间的未对准情况。因此,完全密封并润滑的齿条接头能够可靠地防止使用寿命内磨蚀情况的发生。
第二代eAxle配有一个差速器,该差速器的性能已得到提升,可满足更高扭矩要求。
差速技术
电子断开差速器(EDD)
在驾驶模式中,如果不需要后桥运转,可将电动机与传动系统断开。断开功能可由集成到开放式差速器内的独特爪形离合器断开装置实现。该系统由一个电磁体驱动,并使用霍尔传感器对离合器位置进行无触点式检测。
电子断开差速器(EDD)自2012年起就开始成功地批量生产,当时标致3008使用的就是这款差速器。
图7显示的是连接及断开驱动情况下的旋转组件。
图7 :连接及断开驱动模式下的旋转部件
断开离合器确保在需要将总效率最大化、降低拖拽扭矩以及防止电动机过度旋转的任何时候,均可以将电动机断开,例如:当车辆仅由内燃机驱动以较高速度运转时。
图8显示的是电子断开差速器(EDD)的系统全貌。
图8:电子断开差速器的系统全貌
断开离合器由低电耗的小型电磁体驱动。电磁体的设计以及周围组件材质的设计和选择均以相互匹配为原则,以优化驱动离合器的磁力。
电磁体通电后,其柱塞马上会将带有传感器摩擦片的凸轮环以轴向推至爪形离合器,从而完成差速器与最终驱动装置的连接。为实现顺畅安静的接合,电动机会在电磁体通电之前与齿轮系的速度保持同步。该系统的设计方式最低用1A的电流即可维持连接位置。当电流切断且电动机扭矩下降时,碟形弹簧会将凸轮环推回至断开位置,因此系统的失效模式是“断开"接合时间约75毫秒(不考虑齿到齿的位置) ,断开时间约30毫秒,这都证明了EDD具有出众动力性能。若将差速器从齿圈断开,可使拖曳损失降至最低,从而实现断开模式下卓越的传动系统效率。
吉凯恩这款已获专利的独特EDD可提供:
极低的断开拖曳扭矩
重量轻、结构紧凑
接合时耗电少断开时不耗电
接合及断开时间短
失效保护断开模式
断开装置的性能己通过模拟进行优化处理。试验台及车辆测试均证实了系统的出色动力。断开系统的快速驱动可使混合动力系统的控制策略得到增强,从而以最佳的整体系统效率以及最节油的方式优化了混合动力及AWD应用和性能。
在效率及NVH方面优化齿轮系
效率
最低效率以及随后对整个eAxle效率进行优化是车辆规格的基本要求,以实现纯电动模式及混合动力模式下的预期续航里程。
在讨论按需式混合动力车辆的效率时,这意味着要考虑两种操作模式:
连接模式下的电力驱动装置→关键测量指标: 齿轮箱以扭矩和速度为参数的效率。
断开模式下的电力驱动装置→关键测量指标; 断开时齿轮箱的拖拽扭矩。
尤其需要注意的是,以下损失会影响齿轮箱的整体效率。将这些影响因素所带来的负面影响降到最低,这是一项极其重要的开发任务。
齿轮啮合损失
搅油损失
轴承损失
密封损失
此外,为确保连接驱动模式下能达到出众效率,开发了一个被动油润滑系统,避免了因增加油泵带来的能耗。
图9显示的是驱动模式下不同输入扭矩值的效率测量结果。对于33Nm以上的所有扭矩值,测得的效率均超过了97.5%。
图9: 40℃时不同输人扭矩值的效率测试结果,驱动模式
图10报告了滑行模式下不同输入扯矩值的效率测量结果。
图10: 40℃时不同输入扭矩值的效率测试结果,滑行模式
齿轮系在驱动和消行两种模式下的最商效率均得到了优化,模拟和测定结果均证实,在驱动和滑行模式下的效率处于同样高的水平,这个结果对混合动力的动力总成架构而言至关重要,齿轮系效率的每一次改进均会带来双重好处:驱动,制动和给电池充电期间的能量回收。
由于吉凯恩独特的断开差速器功能原理,拖拽扭矩在断开模式下处于极低水平。齿轮系分离开且保持停止运转状态之后,就不会有转动的齿轮啮合及搅油损失, 也就意味着总损失会降至最低。断开状态下的拖拽扭矩经测量在2.5Nm以下,这个数值比连接模式下的拖拽扭矩大约低80%
图11显示的是接合模式与分离模式下拖拽扭矩的测量结果对比。
图11:拖拽扭矩测量,接合状态与分离状态
NVH
随着动力总成系统不断向电气化方面发展,汽车制造商越来越重视不必要的噪音排放和声学优化。如果缺少对声音的掩蔽,特别是在较低速度范围运转时,配备内燃机的车辆内将会听到与之不相干的噪声,并且可以判断为烦人的噪音。为满足要求以及最终客户对周围噪音的期望,现已将开发计划的主要关注点集中在NVH性能方面。
14000rpm的输入速度为变速器的噪音排放提出了富于挑战性的要求。借助模拟工具对齿轮系进行优化以及在实验台进行验证,可在较大的运转范围内实现降噪。
为实现杰出的NVH性能,对以下各项进行了详细调查:
系统级轴的布局
包括啮合阶次分离的齿轮宏观调查
用于修正的齿轮微观调查
变速器误差最小化,包括制造公差的敏感性
前景展望
车辆制造商致力于对其整个产品组合进行电气化,这一趋势为吉凯恩传动系统的eDrive系统发展历程开启了令人振奋的篇章。一方面,相关法规要求降低车辆的二氧化碳排放量,另一方面,客户对AWD车辆的出众驱动性能及安全性的期望越来越高。即将到来的车辆排放测试周期会加快混合动力车动力总成架构的普及。
如果车辆制造商采用吉凯恩的eAxle技术,那么它们提供的插电式混合动力车辆的价格会与现有车辆的价格处于同一区间。
吉凯恩传动系统已经生产了30多万台eAxle,并且还在继续研发下一代技术,以满足更高扭矩要求,实现eDrive模块与驻车制动的全面集成。未来的发展不仅会关注硬件组件,而且会把重心转向系统开发、控制和集成。
此外,根据提出的概念以及已确定的吉凯恩Twinster技术,吉凯恩开发出了eTwinster概念,此概念利用一个电力驱动系统首次实现了全扭矩矢量控制,并且在提供突出驱动性能的同时减少了二氧化碳排放量。采用此技术的试驾版汽车已经在2016年冬季测试中的试车跑道上得到成功展示。
作者:
Dipl.-Ing. Anja Häniche
Dipl.-Ing.(FH) Marc Absenger
GKN Driveline International GmbH(德国洛马尔)
Andreas Mair 博士 吉凯恩传动系统(意大利布鲁内克)
版权归原作者及其所属单位所有,转发请注明相关信息。
参考文献:
Juraschek, S.; Vachenauer Dr., R., Lorenz, K.; Marschall, T.; Stephan, A.; Tachtler, J.
全新宝马 2 系 Active Tourer eDrive 搭载高效插电式混合驱动系统