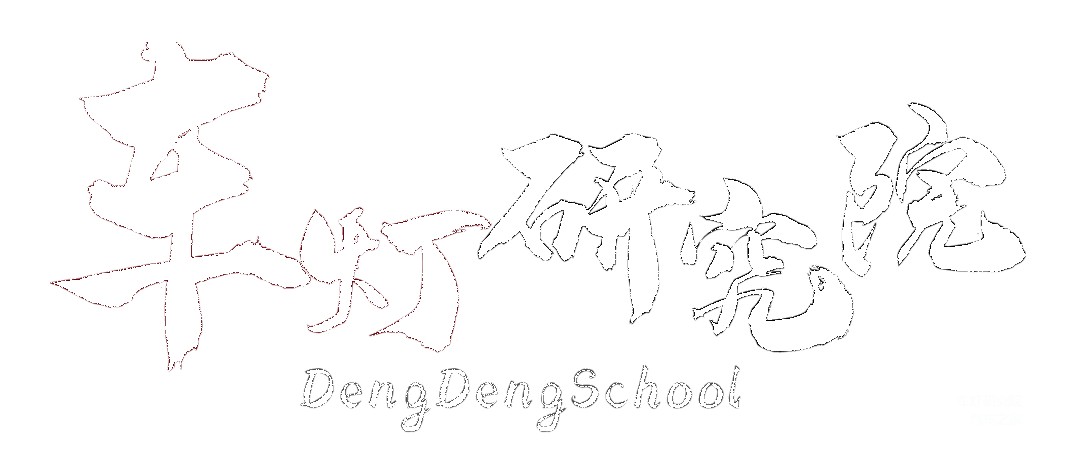
当我们分析现今各大车展或技术论坛关于下一代车灯的设计潮流时,有一个无法回避的趋势,即是车灯的扁平化。特别是一些新能源车型上,由于取消了前格栅,两只”眯眼”越来越窄,格外夺目。
同时各大车厂发布的概念车也越来越多的采用扁平化的设计。
(Acura 2016 Precision Concept)
(BMW 2019 Vision M Next Concept )
(Jaguar 2020 Vision Gran Turismo SV Concept )
(Changan Vision V concept)
(SAIC Roewe R-Aura concept)
(GAC ENPULSE concept sport car)
(FAW T²Concept)
Section 1
薄透镜车灯的技术现状
从市场趋势分析可以看出,扁平化是汽车造型设计的主要趋势之一。之前仅仅是日行灯或位置灯采用这种设计,现在连远近光也采用这个设计趋势。远近光透镜模组不再是传统的半圆球型,外观也越来越薄,越来越纤细,而且每个大灯内的模组数量也有增加的趋势。
为了应对这一趋势,势必对现今的远近光模组的设计和生产提出许多挑战,因为模组的尺寸和光学效率是息息相关的。透镜模组高度越小,光学效率势必越低。而车灯是汽车行车安全和舒适非常重要的零部件,其光学性能无法妥协,相反IIHS和CNCAP的相继引入逐步提高了车灯照明安全的重要性。同时现在大灯往往被要求远近光集成更多的功能(如ADB, 道路投影等),近光不再是一个静态的光型,而远光也增加了防眩目功能,用来应对各种复杂的天气、道路情况和交通状况。
在光学性能维持不变甚至上升的前提下,光学效率的降低则意味着功率的上升和CO2的排放增加。现在全球都在致力于减少碳排放,很多国家和企业都制定了雄心勃勃的碳中和远景目标,比如中国承诺在2060年前实现碳中和。因此在减少碳排放的压力下,薄透镜远近光模组迫切需要更高效的光学方案。
我们随机拆开现有市场上的一个常见远近光透镜模组(如下图),通常从功能上可以分成两个组件,一个固定的led光源底座和一个活动的透镜组件。光源底座为一排并列的led光源安装在铝制散热器上,活动的透镜组件一般又可以再拆分为2个光学零件,即一个光学外透镜和一个全反射的光学聚光内透镜或者镀铝的反光镜,采用全反射内透镜或反光镜完全取决于灯厂的技术方案和性能要求,整体上差别不大。整个模组的光学性能的关键是如何使这两个组件更好的匹配起来,形成所需要的远近光光型,并保证整个模组的光学效率。
(双功能模组的爆炸图,上图为近光光路图,下图为远光的光路图。)
上图的光学模组采用了一个70mm x 50mm的外透镜,从光路原理上可以看出,单纯的增大或缩小外透镜的尺寸基本上不会改变光路分布,但是由于外透镜尺寸变化,模组的光通量和光强的值会同比例的改变。为了弥补光通量和光强的变化,一般可以通过改变led的数量和改变单颗led的光输出这2个技术手段,通常这2个技术手段对大部分的透镜尺寸都有效,但是当透镜尺寸缩小到某个临界点时,以上2个手段就失去了作用,因为这时不仅光通量和光强会变小,而且整个远近光的光路被压缩而导致失去部分功能。比如,当70mm x 50mm的双光模组在缩小到60mm x 40mm 仍然有效,但是在60mm x 30mm 时,这时双光模组仅能实现一个近光功能,因为大部分的远光光路都丧失了。当透镜尺寸过小,这时现有的光学方案已经不再可行。特别是对于一些高端的模组,比如矩阵模组、像素模组,往往需要更大的透镜Z向尺寸,薄透镜大灯更加具有挑战性
下图则显示了远近光模组尺寸的一个演化过程,开始都是和卤素模组/氙灯模组一样的圆形Led透镜模组,后来在高度方向上越变越小,现在市面上的薄透镜模组的最小高度通常为30mm –40mm,随着技术优化可以近一步的缩小到20mm。如果要进一步优化到15mm甚至10mm 则需要更创新的方案。
(透镜模组的尺寸变化趋势)
Section 2
薄透镜车灯的技术突破
上面已经介绍了薄透镜车灯的挑战主要是主照明功能光学效率的降低。为了提高光学效率,仅仅通过增加LED的光通量是不够的,因为这受到了led技术本身的散热、功耗和成本的限制。因此还需要从其它方向加以改进。
第一个方案为增加防反射涂层。防反射涂层可以有效的提高透镜模组的光学效率。通常情况下,每次不同材料间的光穿透都会因为光反射损失光能量的4%左右。如果透镜模组有2个透明光学零件,则不同材料间的光穿透有4次。因此,理论上通过涂防反射涂层可以获得约16%的效率提升。虽然防反射涂层的工艺已经成熟,但是在前照灯透镜模组中的应用仍有很多挑战,因为led光源的高温会损害涂层并且熔化透明光学件的微结构。扁平透镜模组和椭圆透镜模组内的透明光学件的形状大相径庭,因此涂层的工艺处理非常复杂。但是一旦模组供应商突破了工艺上的难点,能够找到一个好的涂层解决方案,那么这个方案也可以应用在其它的透镜模块上。
第二个方案为增加 LED的光强。使用尺寸更小的led芯片,这样其他光学零件的尺寸也可以相应地缩小,例如激光光源可以用在高亮度的辅助远光上。虽然现在每一代LED芯片的亮度越来越高,但是这一趋势总是有天花板的,因为光学内透镜的材料大多是塑料的,塑料材料的耐温等级是有限制的。因此在某些特定的透镜模组里,使用玻璃透镜或者镀铝反光镜来解决这一耐温问题。甚至一些更先进的透镜模组,比如矩阵或像素模组,使用了硅胶透镜。硅胶可以被加工成复杂精细的形状,同时能承受更高的温度。
对于大多数的led透镜模组而言,比如双功能模组或单行矩阵模组,通过使用上面的解决方案,基本上可以将led透镜模组的高度降低到20mm左右。如果还需要做得更薄,比如超薄透镜模组,则需要考虑下面的一些解决方案。
第三个方案为使用一体化内透镜。比如下图显示的是一体化透镜模组的一个例子。它的2个透镜模组的高度是27mm,光学效率可以>50%,性能已经非常不错。虽然当初是一个定制的模组光学方案,但是随着市场的需求扩大,这个方案已经被大量的应用于超薄透镜模块的设计上。
(一体化光学方案的一对模组;左边是截止线近光模组,右边是广角近光模组)
这套模组内的核心主光学零件是一个一体化的光学内透镜,它能同时完成三个任务。首先将LED光源的光通过全反射收集并引导到截止线平面上,截止线平面位于一体化光学内透镜的焦点处。其次在截止线平面上,光被修整成截止线光型。最后再将截止线光型从出光侧投影到路面上。
这套透镜模块有着较高的光学效率。因为全反射收集的光几乎没有损失。其次,整套光学系统只有一个透明光学零件,没有不同材料间的光穿透,因此没有菲涅耳光学损失。
一体化光学模组的主要挑战是一体化光学透明内透镜的复杂形状,使得注塑工艺非常具有难度。不过一旦模组供应商解决了一体化内透镜的注塑问题,由于所有光学都在同一个塑料透镜内,因此整个模组的装配就非常的简单和可靠。通过试制的光学样件的测试可以证明,使用这项技术可以将透镜高度降低到15毫米左右,同时保证>40%的光学效率。
第四个方案为使用MLA。微透镜阵列(MLA)是现今汽车领域广为人知的一项技术。这项技术已经在一些特殊的场景下量产,比如照亮路面的车门地毯灯。到目前为止,MLA的性能还不足以满足远近光照明的需求,但是已经非常接近了。首先,通过全反射光学内透镜将并排的LED光收集,然后将光照在由两个MLA透镜夹成的三明治上,三明治的夹层是一个截止线平面层。靠近led光源的MLA透镜将光聚焦在截止线平面上,截止线平面上有许多几百微米大小的截止线微切口。然后,第二层MLA透镜再将截止线光型投影到路面上。
MLA技术可以实现高度<10mm的模组。而且模组的深度很低,从led光源到模组透镜外表面的距离<20mm。而现在主流的近光模组在深度方向上通常>100mm。因此MLA模组的体积具有碾压优势。同时由于每个微MLA透镜形成的是完整光型,因此该模组的造型设计可以非常灵活。如果MLA透镜足够大,理论上可以将该透镜切割成任何形状,从而得到需要的各种异形模组
MLA技术的最大瓶颈是产生远近光光型的MLA夹层。因为要求的热应力和机械应力非常高。一旦这个瓶颈得到解决,这项技术将在性能和尺寸方面开创一个新的时代。
Section 3
薄透镜车灯的总结和展望
以上我们总结了当前薄透镜模组的各种技术特点和改进方案,使用前2种方案基本上可以使模组高度降到20mm左右,而使用后面的这两个方案有望使透镜模组尺寸减小到15mm和10mm,这基本上可以满足大多数车厂客户的前大灯造型设计要求。如果还想进一步的减小模组高度,则需要牺牲整个模组的光学效率。而实际应用中,具体使用哪一种方案是最佳方案,则取决于车厂的需求和灯厂的技术能力。对于特殊的高亮度模组和矩阵模组,则有可能需要结合以上所有的光学改进方案。
不得不说,外观设计越来越成为当下汽车消费的首要考虑因素,“眯眯眼”的车灯越来越多,不知会不会成为你下次购车首选的风格呢?