很多人不喜欢出门撞衫,穿搭妆面都要“自我”。但选车上又不能太过小众,否则质量品质不稳定的同时,修车养车都是问题。——于是主流品牌的个性化车型便应运而生,比如奥迪Q2L。
Q2L刚上市的时候,我还被闺蜜约着专门去4S店里看车:精致外观、高明度的颜色、个性化的选装件,C柱上明晃晃的四个圈,再加上奥迪家独有的秩序感, Q2L有种都市青春小说里女主的气质:出身正统、善良明媚、又满是古灵精怪的小心思。
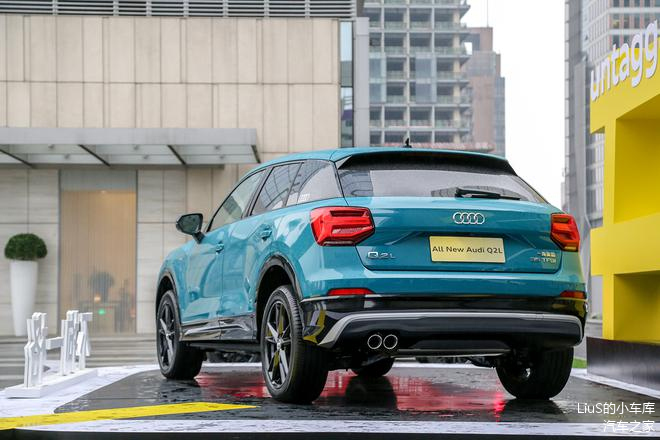
回到问题,一辆奥迪Q2L是如何诞生的?从流程上讲,钢板/铝板进入汽车工厂,经过冲压、焊接、涂装,变成一辆车的车身骨架之后进入总装车间,在这里与装配动力系统、底盘悬架、内饰座椅、电子设备等各种零部件,最后再在质检部门手里被从内到外查验一番——一辆车便如此诞生了。流程上讲奥迪Q2L也是这样,然而细究起来,不同品牌不同工厂不同车型的制造上,也是各有各的特点,来从工厂角度聊聊Q2L的生产吧。
1、“她的家在佛山,智慧工厂啊~~”
以前总觉得所有国产奥迪的车型都是“我的家在东北”,来源于汽车城长春。
其实不然。一汽奥迪在国内有长春(A4L、A6L、Q5L车型)、青岛(Q3车型)和佛山(A3和Q2L)三个制造基地。
其中佛山工厂是一汽-大众在华南的生产制造基地,两期建设的工厂共有年产60万辆的能力,奥迪Q2L正是在这里造的。作为一个智慧工厂,同时在这里诞生的还有Q2L电动版以及ID.4 CROZZ等。
佛山工厂是大众在全球的标杆工厂,智慧工厂的新示范,也是大众旗下全球第一个满足MQB模块化的工厂。
现代智慧工厂嘛,讲求“高效生产”和“可持续发展”两面兼顾,汽车工厂早已看不见冲天的烟筒,反倒是明晃晃的大面积太阳能板让人印象深刻:据说建成后全厂光伏年发电量可超3000万度,每年节约电费超700万元,每年减少二氧化碳排放约2.9万吨。生活和工业污水更是早已实现了零排放——汽车行业在环保方面走得很靠前。
2、就从“高效生产”开始
大众/奥迪可以算是国内卖的好的合资品牌,这样的销量自然需要相应的产量予以保证。在佛山工厂,满负荷生产可以做到65JPH,也就是一个小时生产65台车下线,平均每分钟就有1台车下线。每天有1400台卡车开进佛山工厂,运送7000个大箱和16000个小箱进入车间,85%的零件能在20分钟内到达——而且与之前很多人的认知不同,零件并非是一早就运进工厂囤起来,而是“准时化供货”,比如每台车对应的座椅,是由座椅供应商通过车身的配置信息即时备货,提前1小时送到总装车间座椅排序线上。这样零件错误率低、降低了库存周期、节约零件面积,也节约了成本。
相对应越来越精准的供货,生产线上通过AGV机器人自动导引运输设备、SHOOTER器具对接技术、RFID零件自动入库、PTL料架亮灯式灯光拣选——一系列智能化自动化运输线,不但减轻了人力成本,而且机器的效率和正确率更高,将停台的风险降低了50%,换箱效率提升10%。
现在最新的智能物流系统,AGV小车不但能按照编写好的程序迅速而有序的把零件送到指定工位,新一代AGV还可以进行数据收集,综合智能化库房系统,做大数据分析,根据实际生产情况,自动分析各类数据的内在联系,可以提前预警,使零件既不过盈又不紧缺。
这样的效率、同时要保证稳定的品质,生产环节的高自动化率不可少。
焊装车间有超过800台焊装机器人,自动化率超过70%,6条主焊线自动化率也是达到了100%,焊装整线设计能力是每小时60台下线——也是平均一分钟一辆的速度。
在总装车间,每辆车两万多个零件在这里结合——生产线的布局是个小写的h型,这是以往工程师们经过80多年的生产实践得出来的他们认为最合理的生产布局,一方面节约占地面积,更能减少输送距离,提高设备的运行效率。
总装车间工序繁杂分散,也是需要人工最多的车间,每个工位都有进行优化的可能,比如在总装车间最浪漫的工位:marriage(也就是底盘和车身结合的工位),车身和底盘全自动化结合之后,52个螺栓全部采用电控拧紧机,保证精度,一次性完成。
再比如工程师提到轮胎拧紧工艺:
每台车相对应的轮胎是在装配钱1个小时送来车间轮胎排序线,由轮胎排序线设备自动分成3条线供应到生产线旁,左侧、右侧、备胎,轮胎到了生产线旁后,会由举升设备缓缓降落,同时,轮胎抓取设备会自动行走到举升设备旁,进行轮胎抓取。抓取完后,抓取设备将轮胎运送至车身附近,工人仅仅需要操纵设备进行拧紧,全程行走浪费非常少,绝对是精益生产。每个轮胎螺钉的拧紧数据会处于拧紧系统的监控之下,数据保存15年。
车身下面承托车辆的设备是滑板运输线,每块滑板长度正好覆盖一个工位,每块能承载2.8吨的重量,同时可进行1.45m的可调举升范围,为每个操作岗位调试合适的车身高度,所以工人们几乎不需要弯腰、踮脚等情况,减少疲劳,提升效率。
3、“柔性化”是现在工厂的主题
工业4.0时代的现代化工厂,除了“高效”,还需要“柔性化”来应对各种车型的共线生产和Q2L丰富的定制化配置。
汽车刚刚诞生的时候,都是手工作坊买个底盘回来,按照车主的需求造个车身上去,每辆车都手工打造、与众不同。而福特T型车的出现改变了整个汽车行业——流水线工厂出现,大大拉高了产量,也稳定了品质,甚至T型车只生产黑色一种颜色,化繁为简,让当年的福特在汽车大生产的萌芽时代一骑绝尘。
然而风水轮流转,一百年之后的今天,在早已解决了产线速度和品质稳定性之后,要满足消费者蠢蠢欲动的“自我”,个性化配置、柔性化生产,应运而生。
比如总装车间要同时共线生产各种配置的Q2L,而这款车型本身的个性化配置十分丰富:超过5万种个性化搭配、双色顶盖、定制C柱装饰、光座椅的配色就有8种选择……在流水线上可能这辆是冰川白双色车身中配车型,下一辆就是珊瑚橙顶配车型——完全按需生产,自由排队。
汽车行业的总装车间很早就实现了柔性化生产,而佛山工厂让人印象深刻的是焊接车间的柔性化——可以算是全球柔性化度最高的焊装车间,采用3个康采恩框架,能够实现至少4种车型、最多8种车型的混线生产。
所谓康采恩,是全球独有的柔性化生产技术:当某个车型即将到达这个工位的时候,智能生产系统就会得到指令,提前准备相应的车身框架,来进行相应的生产。夹具系统能够在车身上实现多达50余处的尺寸加紧,40个气缸用于定位,同时多达12台机器人同时进行焊接工作,在51秒之内就可以调用相应的夹具和机器人完成整道工序,安全性达到了SIL3级的标准,这是仅次于核电和高铁的安全等级。
同时,工业4.0下的数字化管理和大数据分析,充分保证了从客户下单的那一刻,就可以追踪到这辆车在流水线上的生产进度,准确得到它应该匹配的零部件和个性化选装件,再到质检、运输,最后送到客户手中。
4、最后,其实消费者对工厂最看重的,大概还是“品质保证”
高效生产+柔性化产线解决了现代化生产的问题,但其实消费者更看重的:是质量的稳定性——内心OS:“我不管你们造的快不快,我就管我买的这辆好不好!”
汽车工厂在质量把控方面也做了大量的工作,尤其是奥迪作为德系豪华品牌,在对质量把控的严苛程度上非常“处女座”。
比如焊接车间有6处激光自动在线测量工位,每个工位有4台机器人,会时刻不停的对生产出来的车身尺寸进行实时监控,监控精度达到0.3mm。当生产出来的车身有偏差,实时监测系统就会发出预警,相关负责人员会马上赶到现场,进行分析和处理,及时解决问题。从生产线的开始到中间过程和最后的交付过程,都有数据监控。
再比如总装车间,生产之后的质检环节全面细致。
静态检查会看是否有外观的坑包、划伤、漆面等;匹配的门间隙、棱线对齐、车门关闭舒适力。内饰里的内部匹配,像仪表板每个按键、旋钮等,甚至是座椅缝线的均匀性,座椅表面角落的一些皱褶、材料质感。
其中,常规车企一般采用线上质检人员手持塞尺等检具进行手工匹配检查,而佛山Q2L采用自动检测机器人对匹配质量进行检查,可实现整车表面、间隙、平度等匹配尺寸在线动态测量,并根据预先设定的公差范围,自动判断是否合格,精度可达0.05mm,比人工用工具的0.1mm精度提升了大半个数量级。以保证Q2L的装配品质。
闯过静态检测,还要经过动态检查,包括多种复杂路况下检查车辆的噪音、行驶过程的通畅性。再到高速路试:检查控制风噪、跑偏、档位、定速巡航等多项功能。每台Q2L交到客户手中之前都要完成整套流程。
5、最后,回到Q2L诞生的第一步
综上,看到这些蠢蠢欲动的朋友们,如果想完全定制一辆自己的Q2L,可以先去官网看看。选好配置可以直接网上点下单,预计交付时间6~8周即可——这是开启奥迪Q2L诞生的第一步。