2021年年底,蜂巢能源在常州举办了以“蜂速·创未来”为主题的第二届电池日发布会。在发布会上,蜂巢提到了自己的领蜂“600”战略,也就是在2025年产能要达到600GWh。
除此之外,蜂巢能源还强调了一个关键词,那就是要推行电动全域短刀化。也就是说“短刀”电池会成为蜂巢能源未来发展的重点,同时也会是未来电动化领域的焦点。
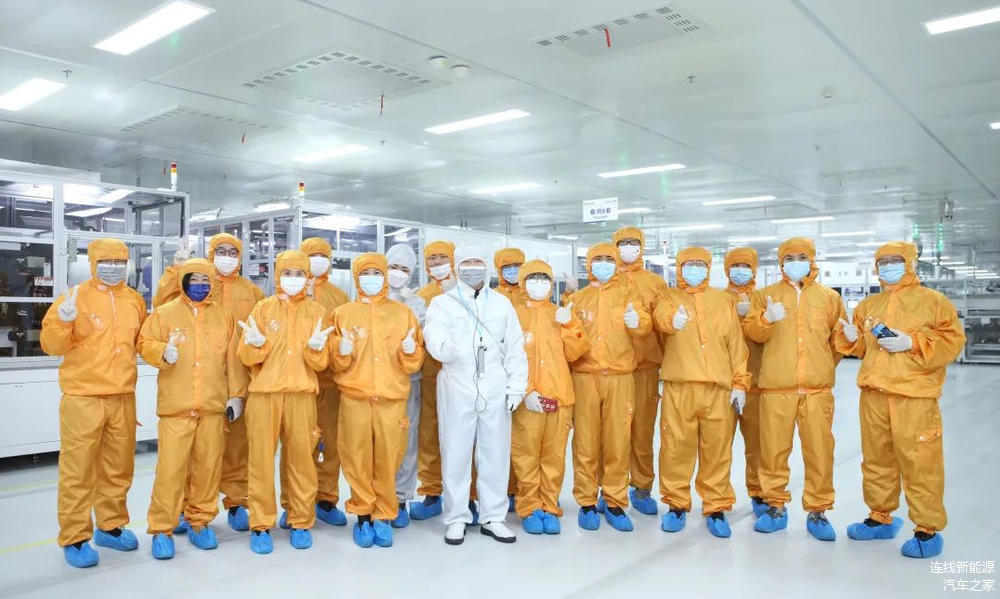
连线新能源当时就找到了大量相关的资料,想探究一下蜂巢这把“短刀”到底潜藏着什么样的奥秘。没想到这刚开年没多久,就等到了机会。
2月25日,连线新能源与其他媒体代表一起受邀参观了蜂巢能源的金坛工厂,得以零距离探访“短刀”电池的智造过程,同时还有机会聆听蜂巢能源工艺资深总监刘小安的解说,以及采访到了蜂巢能源董事长兼CEO杨红新。说实话,整个参观过程大受震撼,也与大家一起分享一下。
01 长薄化是趋势,“短刀”电池可以兼顾内外
蜂巢能源成立于2018年,他们在全球规划了11个生产基地,而常州金坛工厂则是他们的第一工厂,也是公司总部所在地,因此它基本可以代表蜂巢能源制造和生产的最高水准。
金坛工厂总产能规划为68GWh,我们参观的是二期工厂建成的首条“短刀”电池量产线,它的满产产能可以达到2.5GWh,相当于二线动力电池企业的年出货量。
“短刀”片电池拥有非常出色的兼容性和适配性,毕竟这种长薄的形态非常容易成组、成包,相比传统的方形电池,它的散热性更好,安全性也更加出色。同时长薄的设计让它的Z向高度大大增加,尽可能多利用Z向空间,电芯体积利用率提升了15%;而电芯底部则能直接粘接水冷板,让电池包的结构数量减少了35%,从而使能量密度提升了8%。
“短刀”电池的长度可不是将比亚迪的刀片电池缩短,而是充分考虑了市场上的适配性。以蜂巢能源展示的L600电芯为例,它的实际长度其实是574mm,比目前市场上常用590模组要小一点,这让它可以直接兼容现有的590模组方案。基本上可以不用改外包络,就能适配相当多的电动车。
实际上蜂巢能源对于“短刀”电池的各个序列已经有了明确的分工,L600电芯主要是覆盖主流的500~600km续航车型,同时通过果冻电池0热失控技术,它还可以进一步实现800公里续航;L300电芯则是针对2.2~4C快充体系,适配800V高端车型;L400则是针对主打长续航、低成本的PHEV车型,它的能量功率可以兼顾LFP体系,实现高安全和长寿命;L500则是覆盖从储能到商用车领域,并且这些系列的“短刀”电池都能实现平台化生产。
对于蜂巢来说“短刀”电池其实实现了两方面的利好,对内通过平台化的优势规避大规模建厂的投资风险,对外来说重组的效率和成本也大大降低,安全性也是优化的,客户更容易接受。
02 不止是高速叠片工艺,六大工序创新铸就传奇
2021年,蜂巢能源的装机量闯入了全球前十,并且全年装机量增长了足足416.67%。这对于一家成立不到4年的公司来说,确实相当惊人。在参观金坛工厂之前,连线新能源一直以为它们靠的就是行业第一的高速叠片工艺。
结果发现事情的真相远没有那么简单,实际上它们的匀浆、涂布、辊压、模切、叠片、装配六大工序都达到了国际一流水平。
先说匀浆,蜂巢能源采用了2300L大容量双行星搅拌设备,这个设备单体容量达到了国际领先水平,非常适合用于动力电池的大规模生产。每罐浆料可生产约10辆电动车所需要的浆料。这种大型的匀浆设备能更好地保证产品品质,让它在大规模工业化量产中的一致性更好。
蜂巢能源还在匀浆环节设置了三道除磁工序,除磁磁棒的磁通量行业最高,使得浆料级磁性异物含量可以降到50ppb以下,这个数值高出行业平均水平50%。
而到了涂布环节,蜂巢能源则用上了1400mm超宽幅涂布机。它可以一次出两列,涂布速度可以达到80m/min,这同样达到了行业领先水平。蜂巢能源在涂布设备上设置了2套CCD实时涂宽检测系统和三套β射线在线面密度检测系统保障精度,可以将涂布面密度控制在±1.5%以内,涂布正反面错位小于等于0.5mm。
在辊压工序,蜂巢能源可以实现正极热辊压和负极双辊连续滚轧,辊压速度高达80m/min,将电磁加热、在线激光测厚、红外线在线烘烤、废料边去除等技术集成到了一起,实现更高效率。
而在模切工序上,蜂巢能源用上了激光模切,让模切效率由原来的30m/min提升到了40-50m/min,这就相当于40%的效率增益。刘总监还透露,蜂巢的下一个短刀产线工艺集成度会更高,效率也会得到大幅提升。
我们还参观了蜂巢引以为傲的叠片工艺机,之前它的出现对行业带来了极大的冲击力。当前金坛工厂所采用的叠片机效率可以做到0.4s/片,这已经是业内领先水平。
在旁边我们还能看到用格挡围起来的下一代超高速刀片电芯极组成型设备,它的叠片效率可以做到0.125s/片,已经超越了卷绕极组成形效率,也是当前世界上刀片电芯生产效率的最高水平。关于这款新型超高速叠片机,蜂巢已经开始招标产线,即将导入量产。
在叠片完成之后,“短刀”电池会进入极组物流运输环节。由于“短刀”电芯单极组的重量和长度尺寸是其它极组的1到2倍,它的叠片至热压转运过程对齐度的要求相当高,因此蜂巢放弃了传统的皮带物流线,导入了先进的磁悬浮物流线。
这条物流线的价格刘总监没有透露,相信肯定是价格不菲。不过它对传输效率的提高确实立竿见影,达到了传统皮带物流线的10倍,而且由于磁悬浮运输车的加减速更均匀,“短刀”电芯极组的对齐度也得到了保证。由于磁悬浮采用的是润滑滚动,也大大减少了异物的掺入,让电芯的一致性更好,确实是优点多多。
而在装配方面,蜂巢也使出了浑身解数,它在整个电芯装配过程中设置了4次hipot测试,异物检出能力高于行业2-3次,颗粒物检测级别达到了50微米,比行业平均的200微米提升了4倍。针对刀片类电芯最难的周边焊接问题,蜂巢能源用上了行业领先的对缝焊接,正负极同时周边焊接提升效率50%以上,同时,它还用上了超高速焊缝自动追踪焊接工艺,让焊接良品率提升了10%以上,焊接速度达到了惊人的200mm/s。
总而言之,蜂巢能源“短刀”电池的生产线,给人一种“聚沙成塔”的感觉,就是在所有环节都做到了最优、最佳,它的科技创新和投入实在太惊人,实现了超高的生产效率和生产品质。
03 AI智能制造加持,用高成本规避高成本
作为最先进的智能制造工厂之一,我们在“短刀”电池工厂中发现了大量的AI技术应用,它已经与动力电池制造高度融合。
比如蜂巢能源已经采用AI大数据分析进行质量智能检测,它的整个质量检测过程中实现了智能化和无人化,利用人工智能进行不良品的分类,并且可以自动寻找最佳参数,让开发时间节约了大概30%。设备健康管理也实现了智能化,通过先期的预警维护大幅降低故障率,也提高了设备的稼动率。
利用人工智能和边缘/云计算等技术,蜂巢能源大幅提升了生产品质和生产效率,也让整个生产环节可以实现碳追溯。
而根据杨总的介绍,高度智能化工厂的建立居然是为了“省钱”。目的是通过智能化、少人化的设计,实现更高的生产效率,以规避未来的人工成本上涨,从而最终降低制造成本。同时“短刀”电池产线采用的是柔性化的设计,可以从300毫米兼容到500多毫米,这也大幅降低了成本。
通过高度智能化的设计,以及高度规模化的生产,看似投入了大量资金。不过结合蜂巢今年20GWh的出货量目标,以及2025年600GWh,似乎也不必太为他们的过度投入担心。
04 小结
提起蜂巢能源的发展,杨总将之归为技术的胜利。蜂巢的研发投入、资源确实是国内一流的,2018年开始建厂,2022年就要冲击20GWh的出货目标。实际上国内电池行业一发展多年的巨头2021年前出货量才刚刚超过20GWh,可以说蜂巢能源4年的时间取得的发展成果确实相当惊人。