如果说最近车圈谁的热度最高,那一定非“跨界”的华为和小米莫属了。无论是问界炸裂的销量,还是小米玩明白的流量,都让车圈见识到了科技公司加入汽车制造业所蕴含的能量。而就在昨天, 智界S7时隔5个月焕新发布。无论是降价增配的方案、价值3万元的新车主焕新权益还是给老车主的1万元现金红包和平板套装,都点燃了用户的热情。
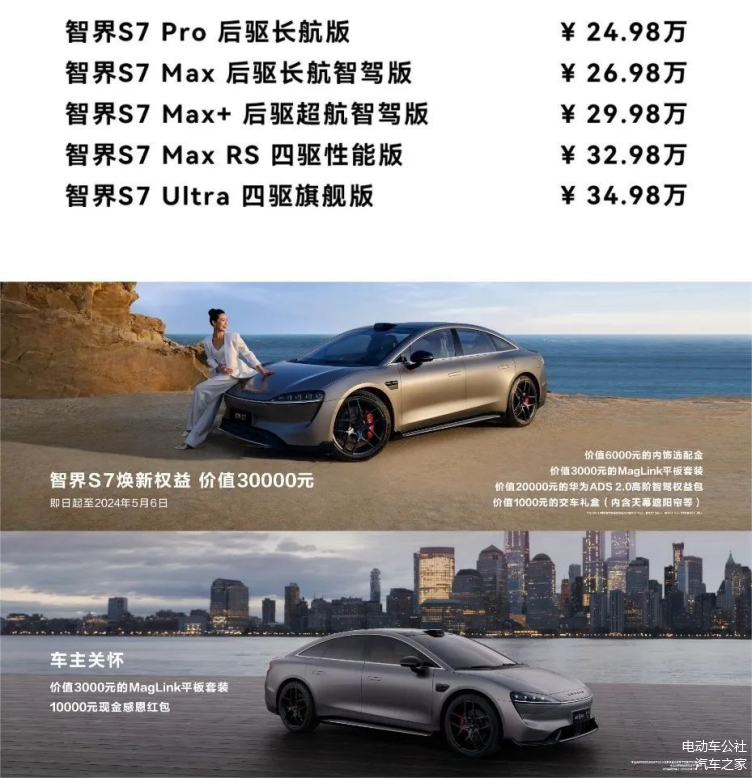
余承东也在现场表示,新车现已开启“海量交付”:
然而仔细回想起来,智界S7在11月28日上市时就凭借“遥遥领先”的破圈力,拿下了2万多台订单。但没过多久,却被车主们在网上发文吐槽交付慢、排产顺序不明确,品控也不稳定,出现了交付瓶颈,随后,智界S7给晚提车的车主们提供了200元/天的补偿方案。
那么今天,我们就来聊一聊汽车制造中质量把控的那些秘密,也深挖一下华为这家科技企业究竟是如何赋能传统制造业的。01. 科技创新,设计为先其实不管是汽车还是其他制造业的商品,都不可避免地需要经历立项-评估-研发-设计-测试-制造-质检的出厂流程,才能把合乎标准的产品交到用户手中。
(始于IBM、发扬于华为的IPD流程,成了很多企业管理者的必修课)但流程中最重要的一项并不是制造,而是设计!先说一个有些反常识的真相——大多数的质量问题并不是制造出来的,而是设计出来的。就拿最近几年3·15曝光的汽车质量缺陷来说吧,今年宝马的传动轴异响,即使是为车主免费更换也无法彻底解决问题,显然是在设计之初就已经“落下了病根”;上一次在2021年爆出的福特变速箱生锈、英菲尼迪QX60失速等情况,也不难从后续厂家的召回计划和补偿方案中看出并不是生产和制造的问题,而是真正的设计缺陷。
因此在制造业中流传着一种说法,设计仅占产品总成本的10%左右,却决定了总成本的70%。用什么规格的零部件,很大程度地决定了最终的BOM成本,也决定了产品的质量,可见设计的重要性。这一点,正是华为所擅长的。华为的智能驾驶之所以能在行业内取得领先,除了软件算法的实力之外,同样离不开对于零部件的精细设计:
智界S7后向毫米波雷达的安装,就通过与后保险杠和油漆精度的匹配,使得对后方来车位置检测精度提升了0.3米以上,也保障了夜晚雨天炫光场景的安全性。而针对车机的黑屏现象,智界S7的鸿蒙座舱也做了不少安全冗余。其将仪表盘和中控屏进行了软件上的隔离,即使车机卡滞也不影响显示驾驶信息,甚至还不会影响智驾功能。就算万一死机了,也会瞬间检测并开启自修复,也就是自动重启。这些,只是华为团队在设计之初就考虑到了产品可靠性,并严格执行设计标准的缩影。
02. 质量是制造出来的前段时间我去了一趟德国,参观了大众的狼堡工厂。无论是占地面积、工厂规模还是男女老少一视同仁的工作机遇、乃至工人专注的工作态度,都给我留下了深刻的印象。但在所谓的先进程度上,还真未必能赶上咱们国内这几年新建的工厂(可见李斌前些年说保时捷工厂不如江淮蔚来工厂,并不算空穴来风)。我们知道,汽车制造的四大车间是冲压、焊装、涂装、总装,也见证着从原材料和零部件到整车的全过程。
考量工厂是否先进的指标,一是生产效率,二是自动化率,三是良品率。而在这几方面,中国的汽车制造业可以说是断崖式领先!智界S7能够在4月开启大批量交付,靠的就是奇瑞芜湖生产基地每分钟下线一辆车的生产速度。算下来,一个月能带来一万多台的产能。这背后,又离不开冲压车间的100%硬件自动化、焊装车间600多台机器人的9大工艺100%自动化、涂装车间167台机器人的100%自动化以及总装车间32台机器人的装配自动化。为数不多需要人力的,要么对冲压的钢板进行复检,确保型面贴合;要么就是在总装线配合机器人装配整车。就连零部件的运输,都几乎全程靠AGV机器人来完成。
在奇瑞打好汽车制造的基础之后,就轮到华为大显身手了。在传统的汽车制造领域中,默认的规则是车企和零部件供应商各司其职,车企只负责组装,零部件的质量由供应商进行保障,也就是以企业效率为先。这就导致了一旦供应商出现问题,反而会导致用户的利益受损,并进一步影响车企的口碑。因造假破产的高田气囊、神户制钢,就都是血淋淋的案例。而华为无论是手机还是新能源车,遵循的都是消费者体验优先。
除了对供应商进行定期检视之外,智界S7的每一批零部件在出厂前都需要进行全方位的检测,把有问题的几率降到最低;在装车前还会再进行一次整车零部件配合的功能性测试,从而保证车辆最终下线时的产品质量。另外,新能源车内部也和手机一样,有着大量的连接线束,总长甚至会达到好几公里,来满足电子电气架构对各个模块的通讯需求。这些“软性连接”的线束位置并不固定,无法通过自动化的机器人进行流水线接插,必须由总装车间的工人进行手工操作,复检也仅能通过目视和触检来进行。
既然是人,就难免出纰漏。会有极少数“中奖”的车辆在行驶几年之后,线束会因为接插失效,导致某些电气零部件失灵(上了年纪的豪华品牌也不能幸免)。因此,智界S7开创性地借鉴了华为在手机制造领域的先进经验,通过AI拍照的方式对接插点位进行检测,并自动和后台数据进行比对,在人工复检的基础上进一步提升检测效率和准确率。从这些案例中不难看出,检验和测试,同样是生产制造中不可或缺的一环。03. 智造的新时代在传统汽车制造领域中,从研发阶段到量产阶段,也都会经历许多轮的全方位测试环节。大家熟知的冬测和夏测、我们曾经做过的续航测试、以及友媒喜欢做的AEB测试,只是车企内部测试中的冰山一角,实际的测试里程和测试科目,远比想象中要多得多!但测试和测试之间,其实也有很大的区别。就拿最简单的整车耐久性测试来说,它的目的就是为了确保车辆在一定公里数的里程内不会出现问题,也涵盖了动力系统、悬架系统、常规路面和特殊路面等多个测试维度。
这里,就有说法了——都是通过测试,但做一套试卷和做10套试卷、60分及格和100分满分的含金量,可是完全不一样的!想要拿满分,一个最简单粗暴的方法就是提高标准。比如智界S7下线前,就需要通过90道检测工序、共9588项检测内容的考验,还要进行全场景超百万公里的耐久性测试,空气弹簧的耐久性要求也是行业的2.69倍。甚至连很多用户一辈子也用不到的酸雨、长时间浸泡、-40℃低温环境,都涵盖在了测试环节里。而在高标准之上还想进一步提升,就需要上一些更加“高级”的手段了,也就是所谓的“智造”。
为了更好地模拟用户实际的用车场景,华为自研了一套自动测试系统,能够在研发阶段对行驶、充电、座舱功能等7000多个项目进行全面的定制化测试,并将数据总结成分析报告。无论是功能覆盖还是测试水平,都称得上一句“遥遥领先”。这样一来,不仅能加快验证周期内的检测速度,还能检测出小概率的质量问题,对硬件本身和软件代码进行全面分析,排查背后的故障点,确保交付后的产品体验。
面对传统汽车制造“发现问题、回溯根源、改进解决”检测流程冗杂、进度缓慢的问题,华为也自主研发了行业独有云端大数据质量检测系统,还对智界S7进行了量身定制。因此在智界S7的生产过程中,每一辆车的零件溯源、来料检测结果、总装过程、乃至试制过程的关键技术数据,都会实时上传到云端的700台高性能服务器上,由系统在第一时间进行风险识别。很多人担心的电池安全风险,也会通过华为自研的AI算法模型进行分析,在危险到来前进行预警。而智界S7的质量管理体系和数字化质量管理,也正式成为华为的ICT产业与汽车制造融合的最佳实践案例。
04. 写在最后华为深度参与造车之后,最大的特点其实是将科技企业的优势和传统制造业的优势融合在了一起。这既是未来发展的方向,也是真正的“中国智造”。包括智界S7在内,许多中国品牌新能源车无论是设计标准、制造标准还是品质把控,都早已不输那些传统豪华品牌。
(在新能源质量排名中获得第一的问界,超过了BBA和特斯拉)而随着智造经验日益丰富、行业间的合作关系越来越密切,我们的新能源车在产品力上也会更进一步,也必将在全球汽车史上写下浓墨重彩的一笔。你我,都是这一历史时刻的见证者。