【汽车轻量化在线】摘要:以轻量化汽车生产需求为导向,通过文献筛选分别归纳出绿色供应商和汽车供应商评价的一般准则,而后基于生命周期评估(life cycle assessment,LCA)找出汽车轻量化需求下绿色供应商评价的关键准则和子准则,并按照可持续维度(经济、环境、社会)进行去重、补充和优化,给出各条子准则对应的轻量化设计方法。研究结果有助于进一步细化子准则,使评价指标更具针对性,对企业提高绿色供应商选择绩效具有积极的参考价值。
关键词:供应商选择;准则分析;轻量化;可持续;汽车产业
汽车零部件供应商的选择,对于汽车制造企业的生产能力、供应链成本和最终赢利均有着直接作用。对于大多数汽车制造企业,其零部件的外购率一般会达到 60%以上,即企业需要将销售额的50%甚至更多来满足零部件采购需求[1] 。因此,如何合理地选择理想供应商,是企业迈向成功的重要一步。
随着全球环境和可持续发展意识的增强,政府的指导和社区知识的推广,企业已经无法忽视可持续性问题在商业运营中的重要性[2-3]。供应链的任一环节都必须在遵守环境标准、满足社会需求的前提下努力保持自身的竞争优势[4-5]。为提高可持续理念的有效性,汽车企业不能局限于产品生命周期末段的循环再利用,而应将行动扩展至初始阶段,例如绿色设计、减少使用危险材料、或车身轻量化以提高燃油效率[6]。对于整车企业来说,这些初始阶段的改进必须通过与零部件供应商的合作才能真正实现。即在选择供应商阶段,企业不仅要考虑采购的零部件本身的质量问题,还要观察供应商是否具有向可持续发展的意愿和能力。然而,在将可持续嵌入日常业务的过程中仍然存在许多困难和挑战[7]。
本文将以汽车轻量化设计为重点,研究整车企业在选择零部件供应商时需要考虑的类别与准则,并将其对应于轻量化设计方法,从而帮助企业从产品设计阶段开始就能融入可持续发展理念,达到优化整个供应链的可持续性的目的。首先,基于轻量化所属范围,从绿色供应商和汽车供应商评价准则的研究中筛选出相关的准则与子准则,并观察其分类方式,随后采用常用的生命周期评估(life cycle assessment,LCA)方法对子准则进行初步分类,在此基础上借鉴可持续维度对结果进行调整和补充,并给出对应的轻量化设计方法。
1 轻量化汽车供应商评价准则筛选
轻量化设计是汽车设计面向可持续发展的热点之一,鉴于其与绿色设计均追求减少环境污染、实现可持续发展的目的,外加具有针对性的供应商评价准则较少,本文将从绿色供应商和汽车供应商两个大方面切入,寻找涉及轻量化设计的相关准则,从而为后续筛选提供参考范围。
1.1 绿色供应商评价准则
早期以Dickson[8]为基础、由Weber[9]发展而逐渐完善的传统供应商评价准则主要集中在价格、质量、交货期上,是可持续发展理念得到重视之前企业最常用的供应商考量标准。直到21世纪初,对于绿色供应商评价或是考虑环境因素的供应商评价研究仍然非常有限[10-12]。
Noci[13]在1997年首次将环境可持续因素融入到供应商评价系统中[14]。他采用层次分析法(analytic hierarchy process,AHP)将供应商环境绩效(environmental performance)评估分为4类,包括绿色能力(green competencies)、当前环境效率(current environmental efficiency)、绿色形象(green image)和净生命周期成本(net life cycle cost)。在此之后,供应商选择问题中的环境可持续评价逐渐发展成为若干准则与子准则[15-18]。Kannan等[19]将绿色供应商选择的评价准则和影响因素进行了适当分类,他们认为在经济可持续方面包含四条准则,即质量、价格、交货期和服务;而环境可持续方面则主要包括环境保护或环境管理、管理系统、污染控制、绿色产品、绿色形象、绿色创新、环境绩效、有害物质管理。可见,根据Kannan等的准则分类方法,传统汽车供应商评价准则的重点——价格、质量、交货期等——基本归属于绿色供应商评价准则的经济可持续分类中,其重要性有所降低。
近期研究认为,虽然生产环保产品或组件能够对供应链的总体盈利产生巨大优势,以社会维度进行实际考量的绿色供应商评价过程也不可小觑[20-23]。同样的,Seuring和Müller[24]、Carter和Easton[25]均提到可持续供应商选择的准则研究集中于环境方面,并且已经作为主要焦点持续了若干年。Ahi和Searcy[26]在有关衡量社会问题的文献综述中指出,可持续供应链的绩效衡量研究中往往忽视了社会因素。作为继经济可持续、环境可持续之后近几年才被纳入到可持续供应链管理中的类别[27],其包含的内容以及衡量方式更具有挑战性,例如健康与安全、歧视、使用童工、国家文化差异产生的工作场所多样化等准则或子准则都难以把握其标准及进行量化。Winter等[28]将若干有关环境供应商选择的文献研究[29-31] 进行了回顾整理,并发现这些研究均只聚焦于环境准则,为此,其检测了企业如何将环境和社会准则应用与供应商选择评价过程,并指出两者之间的重要性有所差异。
1.2 汽车供应商评价准则
汽车供应商评价准则也可分为两个研究发展阶段,其一为传统汽车供应商评价准则,其二为绿色或可持续汽车供应商评价准则。
在节能减排、绿色环保、可持续发展等问题备受关注之前,传统汽车制造整车企业的关注点多集中于与供应商之间的交互,以提升整车质量、维护企业利益为主要目的,其研究所采用的评价准则大多与Dickson[8]和Weber[9]的研究结果一致,即围绕质量、交货期、价格或成本进行补充和展开。除此之外,较常涉及的评价准则还包括产品研发/创新能力、战略合作、企业运营状况、企业信誉、企业竞争力等[32-37]。
石祝竹等[38]从企业实践出发,以供应链管理理论及模型为基础,对现有的汽车供应商评价指标进行优化。原有的评估表将评价指标分为四个维度:质量评定、服务(供货管理、供应商服务、安全)、产品开发问题解决能力(供应商开发能力、供应商开发合作态度、供应商按时提交样件、供应商提交样件质量)、价格,并且分别由不同部门进行评价。研究认为该评价方式需要更加细化,并且应当区分准则的适用范围。在此基础上,优化后的评估指标定为:质量评定(零部件质量、过程能力、质量问题解决、质量持续改进)、服务(供货服务、供应商服务、安全)、产品开发问题解决能力(供应商开发能力、供应商按时提交样件、供应商提交样件质量)、价格,同时将准则的适用范围划分为通用标准、底盘、钣金、内外饰和电器并给予占用分值,使评估表的内容更准确、更具有针对性。
而多数绿色汽车供应商选择研究则同样参照了经济可持续性、环境可持续性、社会可持续性三个维度,并将其中的准则、子准则应用于汽车行业。
Ghadimi等[14]在研究汽车零部件企业由供应链转向可持续性供应链管理的过程中选择供应商时采用的评价标准,并最终制定了一张检查表。作者在整理了其2016年发表的文献综述后,总结出若干环境与社会可持续方面的准则与子准则,并从企业中邀请了四位经理决策者根据相关性从中筛选,得到如下准则结果:环境可持续方面包括环境绩效、绿色形象、污染控制、绿色能力;社会可持续方面则包括健康与安全和员工实践。
类似的,Sch?ggl等[39]也提供了一份检查表,供汽车企业在产品设计的早期阶段评估技术的可持续绩效,其中包括九条准则:资源效率(resource efficiency)、资源消耗(resource consumption)、低影响(low-impact)材料的使用、产品寿命结束(end-of-life,EOL)阶段优化、健康与安全方面、运输与物流、社会与伦理方面、环境污染减少、经济效益和盈利能力。这九条准则涉及绿色供应商选择准则的三个维度之一、之二或全部,所包含的子准则也根据产品设计过程分属不同的生命周期阶段。
从准则上看,绿色供应商评价与汽车供应商评价在可持续性方面具有众多雷同之处,例如绿色能力、污染控制、绿色形象、健康与安全等,其区别大多体现在子准则的详细内容中。而绿色汽车供应商评价准则,则结合了两者的共通之处,并在此基础上细化为适用于汽车产业的具体标准。下文的汽车轻量化供应商评价准则研究,将在绿色汽车供应商评价准则的基础上详细分析针对于轻量化所产生的子准则,并给出具体描述和比较。
2 汽车轻量化的重要性分析
面对有限资源以及环境恶化,汽车制造业必须积极应对市场需求所带来的改变,例如研发与推广新能源汽车、制定标准以衡量产品对环境的影响、选择同样积极承担企业社会责任的供应商进行合作等。而对汽车进行轻量化设计,则能够通过减轻车身或零部件重量,达到节能减排、保护环境的目的,是汽车可持续发展中的研究热点之一。
研究表明,车身质量占汽车总质量的40%左右[40],汽车重量每降低10%,即可减少燃油消耗6%~8%[41]。对于大量使用铝合金的汽车,平均每辆可减重300 kg,同时可在寿命期内降低20%的排放。除了具有减低燃油消耗的优势之外[42],还能够提高加速性和稳定性,改善噪音和振动,缩短制动距离,无论从资源、驾驶还是安全方面考虑,均有益处[43]。可见,汽车轻量化对可持续发展有着重要意义。
目前,轻量化设计的主要方法分为3种:结构轻量化、材料轻量化和工艺轻量化[44-46]。结构轻量化,包括例如汽车结构的尺寸优化、形状优化、拓扑优化和多学科设计优化等方法;材料轻量化,包括采用高强度钢板、轻金属材料(如铝合金、镁合金)、非金属材料(如增强塑料、碳纤维复合材料)等材料减轻车身重量;工艺轻量化,即采用特殊的加工工艺方法,如激光焊接、激光拼焊、液压成型等技术。
由于材料轻量化和工艺轻量化的成本较结构轻量化高很多,许多低成本小排量车的轻量化过程难以大规模采用特殊材料或工艺,必须从结构轻量化技术中寻求突破。而白车身(body-in-white,BIW)的结构轻量化是车身轻量化的核心[47-48],在减轻白车身质量的问题上已具有一定研究成果[49-50]。Mayyas等[51]基于LCA为产品的早期发展阶段研究了一套决策支持性工具,并将其运用于白车身轻量化设计中。左文杰等[45]以弯扭刚度、弯扭强度以及前3阶固有频率为约束条件,以各组件板厚为设计变量,对白车身结构实施了轻量化设计,使白车身质量减轻34.6 kg,减轻率达 11.4%。陈鑫等[52]建立了隐式参数化模型,并利用SFE-Concept参数化建模和多性能优化方法对SUV白车身进行优化,研究各设计变量对车身总体性能的影响,避免了某个性能提高而总体性能下降。季枫等[53]利用灵敏度分析对某三厢车的白车身进行了多学科轻量化优化,优化后白车身总质量降低了19.4 kg,即减轻了6.4%。史国宏等[44]利用方差分析,将某三厢车白车身分成不同的区域,进行了不同工况下的多学科轻量化优化,最终得到的白车身质量降低了12kg,减轻了4.5%。
此外,高云凯等[54]为解决车门系统的各项性能与轻量化之间的矛盾,对车门进行了多目标优化,实现了质量减轻7.99%的同时提高下沉刚度12.18%。朱文峰等[55]以发动机罩板为对象,根据车身结构安全性能要求,建立抗弯和抗扭刚度仿真模型,在满足车身刚度设计规范的前提下实现了发动机罩板减重14.28%。
在新能源汽车领域,同样存在着轻量化设计的问题。尤其是电动汽车行业,由于电池重量过重,降低了电动汽车的有效载荷以及续航里程。为此,谢晖等[56]设定了仿真工况,建立了电动汽车简化模型,将前纵梁的质量优化减轻了11.05%,HIC值降低0.9%,有效解决了前纵梁轻量化后降低电动汽车碰撞安全性问题。朱国华等[57]通过建模预测了复合材料层合板三位弹性性能参数,通过调整渐进失效模型后应用于电动车复合材料车身骨架轻量化设计中,在重量减轻59%的同时表现出更好的耐撞性能。
汽车轻量化的研究关键在于设计与生产阶段,对所用材料、所取结构、所用工艺进行设计和优化,从而使生产出来的汽车满足轻量化、节能减排的要求。因此,整车企业在选择零部件供应商时应当着重寻找具备研发能力、改进能力的供应商,才能满足汽车轻量化设计不断完善的市场。
3 轻量化汽车供应商评价准则研究
轻量化汽车供应商评价准则的划分标准可以根据绿色供应商的三个可持续维度、产品的生命周期、准则属性、或者企业实践经验来进行。其中,LCA是经常用于评价产品或材料对环境影响的方法之一[58-59]。Narasimhan等[60]指出企业向同一家供应商采购的产品可能有若干种,这些产品可能贡献于自己生产产品的不同产品生命周期(product life cycle,PLC)阶段,因此,评价供应商的准则应当根据PLC的阶段特征来确定其重要性。
本文首先根据LCA将准则按照工程设计、生产、使用和EOL4个阶段划分,找到并筛选了其对应的主要子准则(见表1)[14,39,61]。
表1 基于LCA的供应商评价准则
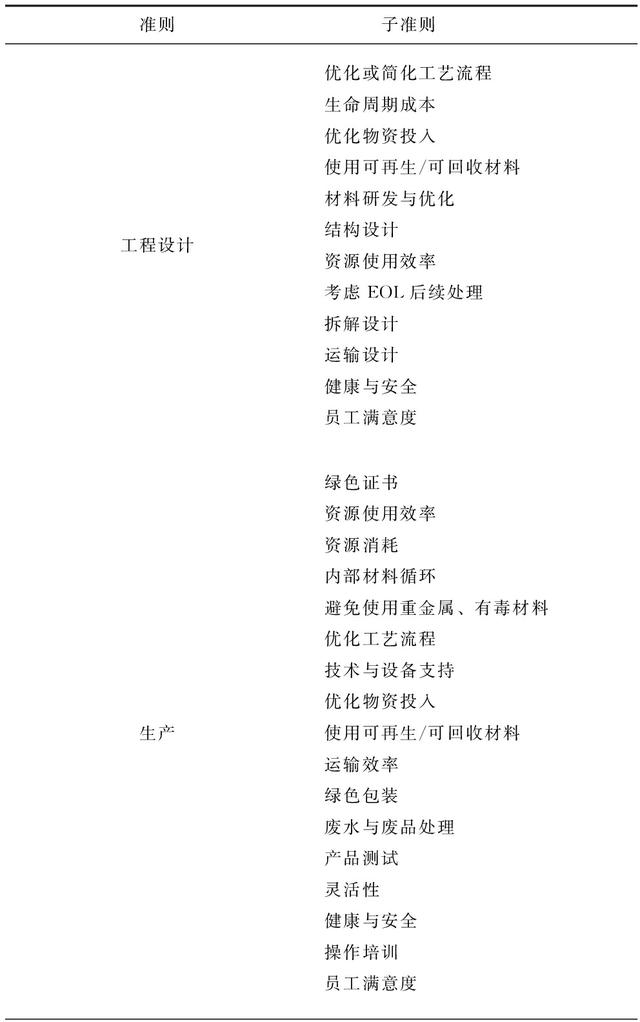
表1(续)
上述的子准则中,有若干旨在达到绿色生产、保护环境的目的,在汽车行业绿色供应商选择中具有普遍性,例如使用可再生可回收材料、资源使用效率、运输设计、废水与废物处理等。而与汽车轻量化设计更直接相关的子准则主要为:
(1)优化或简化工艺流程。评价供应商在工艺轻量化方法中的能力,如是否具备激光焊接、激光拼焊、液压成型的知识储备和技术,是否有能力研究出新的加工工艺以提升轻量化效果。若不能满足,则企业只能转而寻求其他掌握这类加工工艺的供应商或者自己提供生产线进行操作。
(2)材料研发与优化。其对应的是材料轻量化,用于评价供应商是否有能力生产或采购到目前已普遍接受的高强度钢板、合金材料或复合材料等。除此之外,若有意愿与实力同整车企业配合,共同研发新型材料以不断寻求突破,则将得到更优评价。
(3)结构设计。即对应结构轻量化而产生的子准则,主要评估供应商是否有团队主攻结构优化,在现有的材料和工艺基础上研究出更为有效的轻量化结构,包括例如车身形状、厚度尺寸、拓部研究等。该子准则大多出现于产品设计阶段。
(4)灵活性。包括员工灵活性、技术灵活性、设备灵活性等。不同于传统汽车制造业所处的成熟发展阶段,轻量化设计的研发正在快速进步和更迭,其生产流程不断在改进和完善,如此则要求供应商具有高度灵活性以顺应市场需求,例如及时调整工艺技术、采购新型材料、或是置换加工设备等,以此生产出整车企业所需求的车身、缸盖或其他零部件。
(5)操作培训。与供应商的灵活性雷同,轻量化技术的进步将直接体现于技术人员的知识储备量和操作水平上,只有具备一定学习速度、及时开展操作培训,才能在市场中及时调整和优化产出,得到整车企业的青睐。
表1中,有若干子准则在不同准则阶段产生重复,例如使用可再生/可回收材料、健康与安全、员工满意度等。这些子准则的重复出现,一方面体现了其内容的重要性和必要性,即在产品的生命周期中需要屡次考虑以避免设计与实践产生偏差;另一方面则说明基于LCA的分类方式更适用于实际操作时的检查表制定,根据流程一步步评估供应商的完成度,而不适用于支持战略决策。重复的内容使得整车企业在选择供应商时难以快速抓住重点,因此,将子准则按照可持续维度(经济、环境、社会)来划分可能更为有效。表2在表1的基础上将准则与子准则重新划分并进行补充,加入了部分传统与绿色供应商的一般准则,并给出了对应的轻量化设计方法。
表2 基于可持续维度的供应商评价准则
按照可持续维度进行划分后的供应商评价准则,能够更好的按照子准则的属性进行区分,避免重复问题。而依据给定的子准则来评价供应商,则可简化收集数据或评价结果的流程。举例来说,按照LCA的分类结果,企业需要在设计和生产阶段分两次评价供应商在优化工艺流程上的表现,而实际上,整车企业更注重优化后的工艺是否能够有效提高生产效率和轻量化效果,即只需要对最终成果进行评价即可。
当然,本文仅给出了较为常见的子准则,这些子准则本身的评价方式仍然可以得到细化。同样以优化工艺流程为例,其可进一步分为优化工艺可操作性、工艺技术易掌握程度、工艺改进效率、优化工艺成本、设备调整与适应能力等。评价准则的内容越细致,越能够明确其对应的轻量化设计方法。整车企业能够借此根据其轻量化汽车的发展需求有效地筛选评价供应商的关键因素。表2中的若干子准则所对应的轻量化设计方法,意指其可能涉及的内容,对于仅有单一需求(如所售车型只在车身结构上发生变化)的企业来说,在评价该条准则时只需衡量其一即可。
在实际操作中,子准则的分类和细化将根据企业的偏好和需求有所不同,建议将可持续维度作为大类,然后分析其准则与子准则,使用树形图、鱼骨图等方式一步步细化至最根本问题。表2所给出的子准则之间不存在固定的并列关系,应当根据需要适当调整为新的准则、子准则或细化准则,这不仅使决策内容更具有针对性,而且也更容易找到量化方式来进行评估。
4 结论
轻量化设计,已成为传统汽车制造业以及新能源汽车行业的研究热点之一。在避免削弱汽车性能的前提下,通过减轻车身或零部件的重量来实现减少能源消耗、降低排放的效果,从而达到保护环境、可持续发展的目的。其主要方法有结构轻量化、材料轻量化和工艺轻量化。
本文分析了轻量化设计的重要性,并以其为整车企业选择绿色供应商的主旨,分析了基于LCA的供应商选择主要准则和子准则,发现容易出现内容重复问题,不便于企业做决策时进行聚焦。因此,在此基础上将准则与子准则的划分方式重新调整,根据可持续维度(经济、环境、社会)以及准则属性进行调整和补充,得到更为清晰完善的供应商评价准则表,并给出给条子准则所对应的轻量化设计方法,便于整车企业根据生产需求筛选所需内容。
在实际操作上,建议企业进一步细化子准则,为决策过程提供更细致、更具有针对性的评价条目,同时也更容易找到量化方式,以提高决策效率。
来源:期刊-《科技管理研究》
作者:尤筱玥, 雷星晖, 石涌江
单位:同济大学经济与管理学院,剑桥大学制造研究院